27 septembre 2024
Le procédé de sablage est une technologie de traitement de surface très répandue, principalement utilisée pour le nettoyage, l'ébavurage, le meulage et le polissage de divers matériaux tels que les métaux, les plastiques et les céramiques. Avec l'accélération de l'industrialisation, la place du procédé de sablage dans l'industrie manufacturière est devenue de plus en plus importante, en particulier dans les domaines de l'aérospatiale, de l'automobile, de l'électronique et du médical. Cependant, certains problèmes rencontrés dans le processus de sablage, tels que les différences de couleur, de brillance et de rugosité des produits, affectent sérieusement la qualité de l'apparence et la compétitivité des produits sur le marché.
La différence de couleur fait référence à la différence évidente de couleur entre un même lot de produits. Ce phénomène n'affecte pas seulement l'esthétique du produit, mais peut également conduire à l'insatisfaction du client et à des retours. Le manque de brillance donne au produit un aspect visuel non professionnel, tandis que la rugosité inégale peut affecter la performance du produit, en particulier dans les industries qui ont des exigences strictes en matière de qualité de la surface. Ces situations sont très graves. Par conséquent, la compréhension des causes profondes de ces problèmes et la recherche de solutions sont devenues un sujet important pour l'amélioration du processus de sablage actuel.
Dans cet article, j'explorerai en profondeur les causes de la différence de couleur, de la brillance et de l'incohérence de la rugosité dans le processus de sablage, j'analyserai les cas de réussite des entreprises actuelles dans la gestion de ces problèmes et les mesures d'atténuation adoptées lorsqu'ils ne peuvent pas être complètement surmontés. Grâce à une analyse et à une recherche systématiques, il vise à fournir des suggestions et des références pratiques aux entreprises concernées et à promouvoir l'amélioration et l'innovation continues du processus de sablage.
Causes du problème de différence de couleur
La différence de couleur est un problème courant dans le processus de sablage, en particulier pour les produits présentant des exigences esthétiques élevées. Il est essentiel de comprendre les causes des différences de couleur pour améliorer l'effet de sablage et la qualité des produits.
Différences de matières premières
Les matériaux provenant de lots ou de sources différents peuvent présenter des différences de couleur, ce qui est l'une des principales causes des problèmes de différence de couleur. Par exemple, les différents processus de production, formules et conditions de stockage d'une même matière peuvent affecter la couleur de la matière. En outre, des changements dans la composition des matières premières, tels que le type et la proportion d'additifs, peuvent également entraîner des différences dans la couleur du produit final. Il est donc essentiel de garantir l'uniformité de la source et de la composition des matières premières pour réduire les différences de couleur.
Sélection des supports de sablage
Le type et les caractéristiques de l'agent de sablage affectent directement la couleur de la surface après le sablage. Par exemple, l'utilisation d'un agent de sablage à l'oxyde d'aluminium et d'un agent de sablage à la céramique peut produire des brillances et des couleurs de surface différentes. La dureté, la forme et la taille des particules de l'agent de sablage affectent la friction et la rugosité de la surface pendant le sablage, ce qui a une incidence sur l'uniformité de la couleur. Par conséquent, lors de la sélection du support de sablage, il convient de tenir compte de son impact sur la couleur finale.
Modification des paramètres du processus
Les modifications des paramètres du processus de sablage, tels que la pression de sablage, la distance et l'angle, peuvent également affecter de manière significative l'effet de surface après le sablage. Une pression de sablage trop élevée ou trop faible peut entraîner un traitement de surface inégal et donc des différences de couleur. Par exemple, une distance de sablage trop faible peut entraîner une usure excessive à certains endroits, et des angles de sablage différents peuvent entraîner une usure excessive à d'autres endroits. (nous avons déjà écrit à ce sujet), cliquez pour voir) peuvent entraîner des forces d'impact différentes de l'agent de sablage sur la surface, ce qui se traduit par des couleurs incohérentes. Il est donc très important de définir des paramètres de sablage normalisés.
Facteurs environnementaux
Les facteurs environnementaux tels que l'humidité, la température et la lumière influencent également la différence de couleur dans le processus de sablage. Un environnement très humide peut augmenter l'hygroscopicité de l'agent de sablage, modifiant ainsi ses propriétés physiques et affectant l'effet de sablage. En outre, les changements de température peuvent entraîner une dilatation thermique du matériau, ce qui modifie sa couleur. Des conditions d'éclairage différentes peuvent également affecter le jugement visuel de la couleur. Les facteurs environnementaux doivent donc être contrôlés autant que possible pendant le processus de sablage afin de maintenir un effet de traitement cohérent.
Ci-dessous, je montrerai les effets de différentes méthodes de sablage (telles que le sablage à sec et le sablage humide) et leur impact sur la différence de couleur et la brillance afin de vous aider à comprendre l'importance de choisir la bonne méthode.
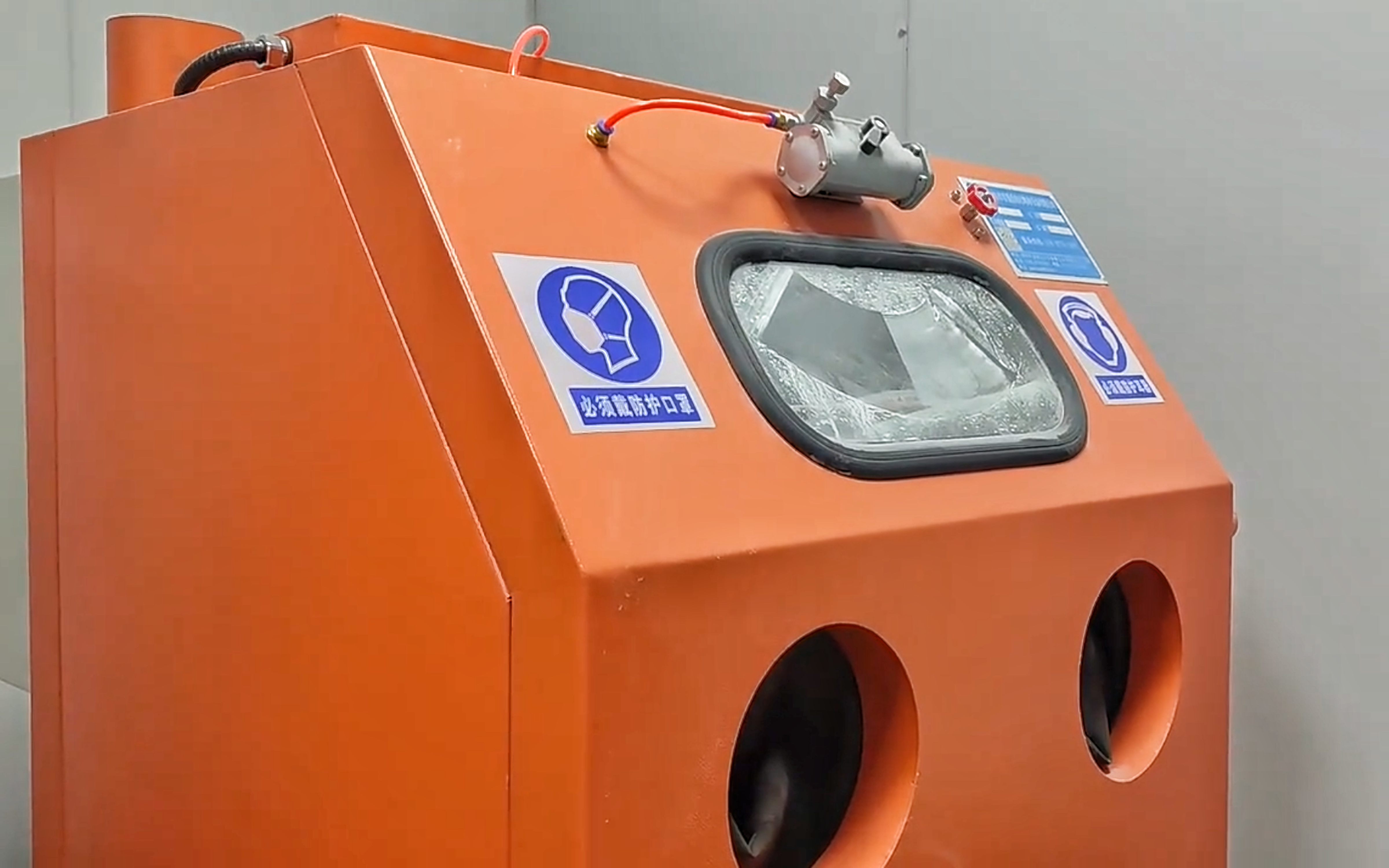
Machine de sablage humide
Aperçu des méthodes de sablage
- Sablage à sec
Caractéristiques : Utilisation d'un média de sablage à sec, adapté à une grande variété de matériaux.
Avantages : Bonne efficacité dans l'élimination des bavures et des salissures, convient aux pièces métalliques.
Inconvénients : Peut entraîner une rugosité élevée de la surface et augmenter le risque de différence de couleur.
- Sablage humide
Caractéristiques : Mélangez de l'eau à l'agent de sablage pour réduire la poussière et la dispersion.
Avantages : Convient aux pièces présentant des exigences élevées en matière de finition de surface et permet de contrôler efficacement la rugosité.
Inconvénients : L'entretien et le traitement de l'équipement sont plus compliqués et le temps de séchage est plus long.
Effet de différence de couleur
- Sablage à sec
En raison du support sec utilisé, une usure inégale peut se produire pendant le sablage, ce qui entraîne des différences de couleur, en particulier lorsqu'il s'agit de surfaces lisses.
Convient pour les cas où la différence de couleur n'est pas nécessaire, mais où un traitement ultérieur peut s'avérer nécessaire pour les applications à forte demande.
- Sablage humide
L'électricité statique générée lors du sablage à sec est réduite par l'intervention de l'eau et peut être répartie plus uniformément sur la surface de la pièce, réduisant ainsi la possibilité de différences de couleur.
Convient aux produits qui nécessitent une grande cohérence, tels que les dispositifs médicaux ou les composants électroniques.
Brillance et rugosité
- Sablage à sec
En raison de la force d'usure élevée, la rugosité de la surface peut augmenter et la brillance peut diminuer.
Ne convient pas aux pièces nécessitant un traitement de surface lisse, telles que les pièces décoratives très brillantes.
- Sablage humide
En réduisant la dispersion du milieu et en améliorant la mouillabilité de la surface, il peut conserver un bon brillant et une faible rugosité après le sablage.
Le sablage humide donne de bons résultats dans les industries qui exigent une grande brillance et une faible rugosité.
Occasions d'application
- Sablage à sec
Convient au nettoyage et à l'ébavurage des surfaces métalliques, souvent utilisé dans l'industrie lourde.
Ne convient pas aux produits ayant des exigences strictes en matière d'apparence.
- Sablage humide
Convient mieux aux produits présentant des exigences élevées en matière de qualité de surface, tels que les pièces de précision, les œuvres d'art et les appareils médicaux.
Convient aux industries ayant des exigences élevées en matière de finition de surface et d'uniformité des pièces à usiner.
En résumé, pour les produits qui nécessitent une grande brillance et une faible rugosité, le sablage par voie humide peut présenter plus d'avantages, tandis que le sablage à sec présente certains avantages en termes d'efficacité et de coût. Il est essentiel de choisir la bonne méthode de sablage en fonction des exigences spécifiques du produit et des normes industrielles.
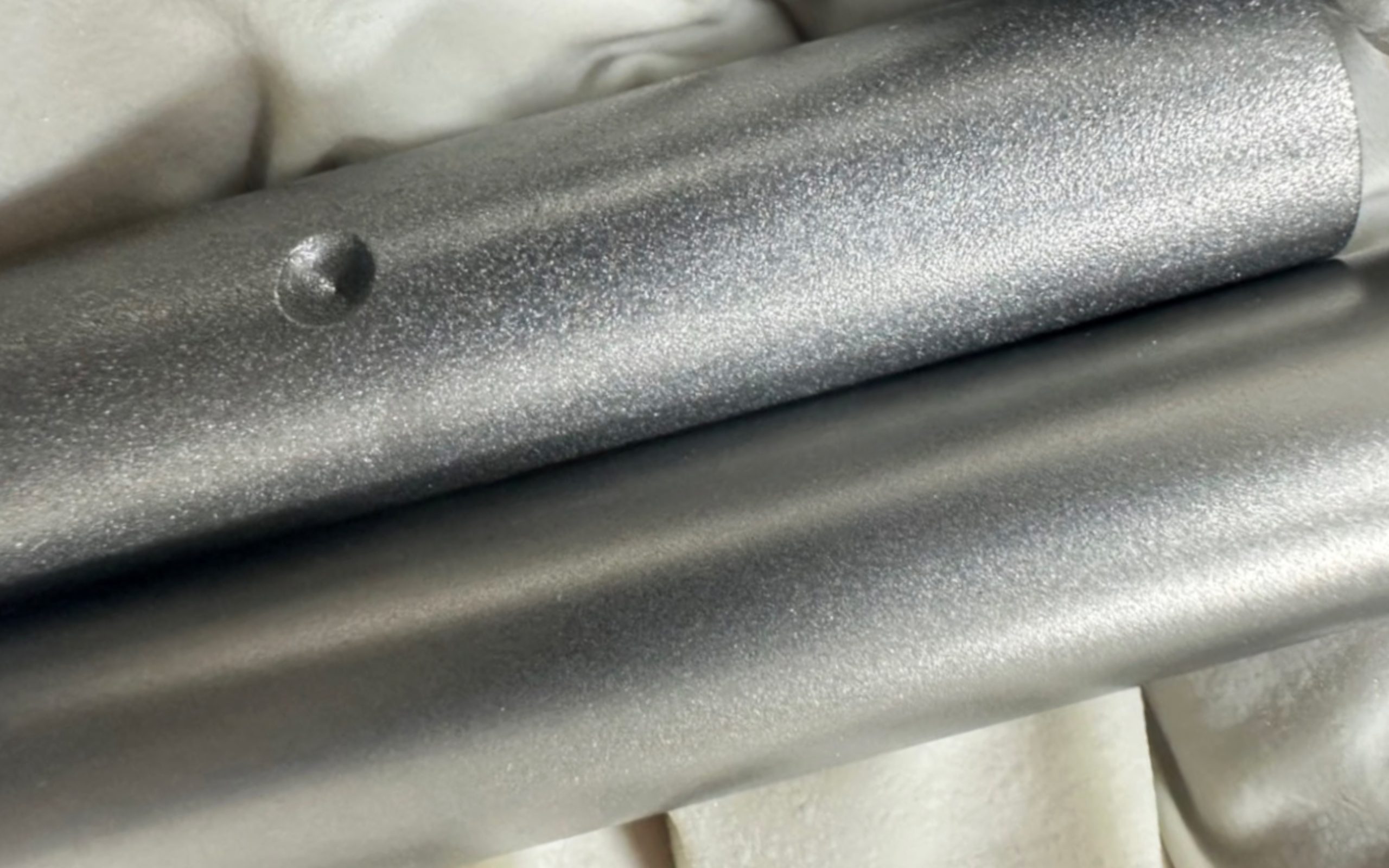
L'effet de différents médias sur la même pièce à usiner
Causes de l'irrégularité de la rugosité
Une rugosité irrégulière n'affecte pas seulement l'esthétique du produit, mais peut également nuire à sa fonctionnalité, en particulier dans les applications qui nécessitent des pièces de précision. Les principales causes d'une rugosité irrégulière sont les suivantes.
Caractéristiques des agents de sablage
La dureté, la forme et la taille des particules de l'agent de sablage ont une incidence directe sur la rugosité. Par exemple, l'utilisation d'abrasifs anguleux peut entraîner une plus grande rugosité de la surface, tandis que les abrasifs sphériques sont plus susceptibles de produire une surface lisse. Par conséquent, lors de la sélection de l'agent de sablage, il convient de tenir compte de l'effet de ses caractéristiques sur la rugosité de la surface.
Incohérences dans le processus de dynamitage
Les incohérences dans le processus de sablage, telles que la distance de sablage, les fluctuations de pression et l'instabilité du flux de produit, peuvent toutes entraîner des variations de la rugosité. Il est essentiel de maintenir la cohérence du processus de sablage pour obtenir une rugosité uniforme.
État de la maintenance des équipements
L'état de maintenance de l'équipement de sablage a également une incidence sur l'effet de sablage. Le vieillissement, l'usure ou la défaillance de l'équipement peuvent entraîner des résultats de sablage instables, ce qui se traduit par une rugosité irrégulière. Par conséquent, l'entretien et l'inspection réguliers de l'équipement de sablage constituent une mesure importante pour garantir la qualité du traitement.
Comment les entreprises existantes surmontent ces problèmes
Dans le processus de sablage, malgré les difficultés liées aux différences de couleur, de brillance et de rugosité, de nombreuses entreprises ont pris une série de mesures efficaces pour surmonter ces problèmes.
Contrôle des matériaux
La sélection de matières premières de haute qualité à partir d'une source unifiée est la base pour assurer la cohérence des effets de sablage. Les entreprises doivent établir des relations de coopération avec des fournisseurs fiables afin de garantir la qualité et la stabilité des matières premières. Cela permet non seulement de réduire les problèmes liés aux différences entre les matériaux, mais aussi d'améliorer la qualité du produit final. En outre, les entreprises doivent veiller à tester et à vérifier rigoureusement les matières premières pour s'assurer qu'elles répondent aux exigences de production.
Production standardisée
L'établissement de paramètres de processus et de procédures d'exploitation stricts est essentiel pour améliorer la cohérence des effets du sablage. Les entreprises doivent clarifier chaque maillon du processus de sablage, y compris la sélection du produit de sablage, la pression de sablage, la distance de sablage et l'angle de la buse. En outre, en établissant un manuel d'exploitation normalisé, chaque opérateur est guidé et normalisé pour garantir la cohérence de chaque opération de sablage, ce qui réduit les fluctuations de qualité dues à des facteurs humains.
Mise à niveau de l'équipement
L'utilisation d'un équipement de sablage avancé peut améliorer de manière significative la cohérence des effets du sablage. Les équipements de sablage modernes sont généralement équipés d'un système de contrôle intelligent capable de régler avec précision les paramètres de sablage et de surveiller en temps réel divers indicateurs pendant le processus de sablage. Les entreprises doivent régulièrement évaluer et mettre à jour leur équipement et adopter de nouvelles technologies adaptées à leurs besoins de production afin d'améliorer l'efficacité de la production et la qualité des produits.
Formation des employés
La formation systématique des opérateurs est une mesure importante pour garantir la stabilité du processus. Les entreprises devraient organiser régulièrement des cours de formation pour aider les employés à comprendre les principes de base du sablage, les méthodes d'utilisation des équipements et les solutions aux problèmes courants. En améliorant le professionnalisme des employés, les entreprises peuvent réduire les erreurs de manipulation et améliorer la stabilité du processus de sablage, garantissant ainsi la constance de la qualité des produits.
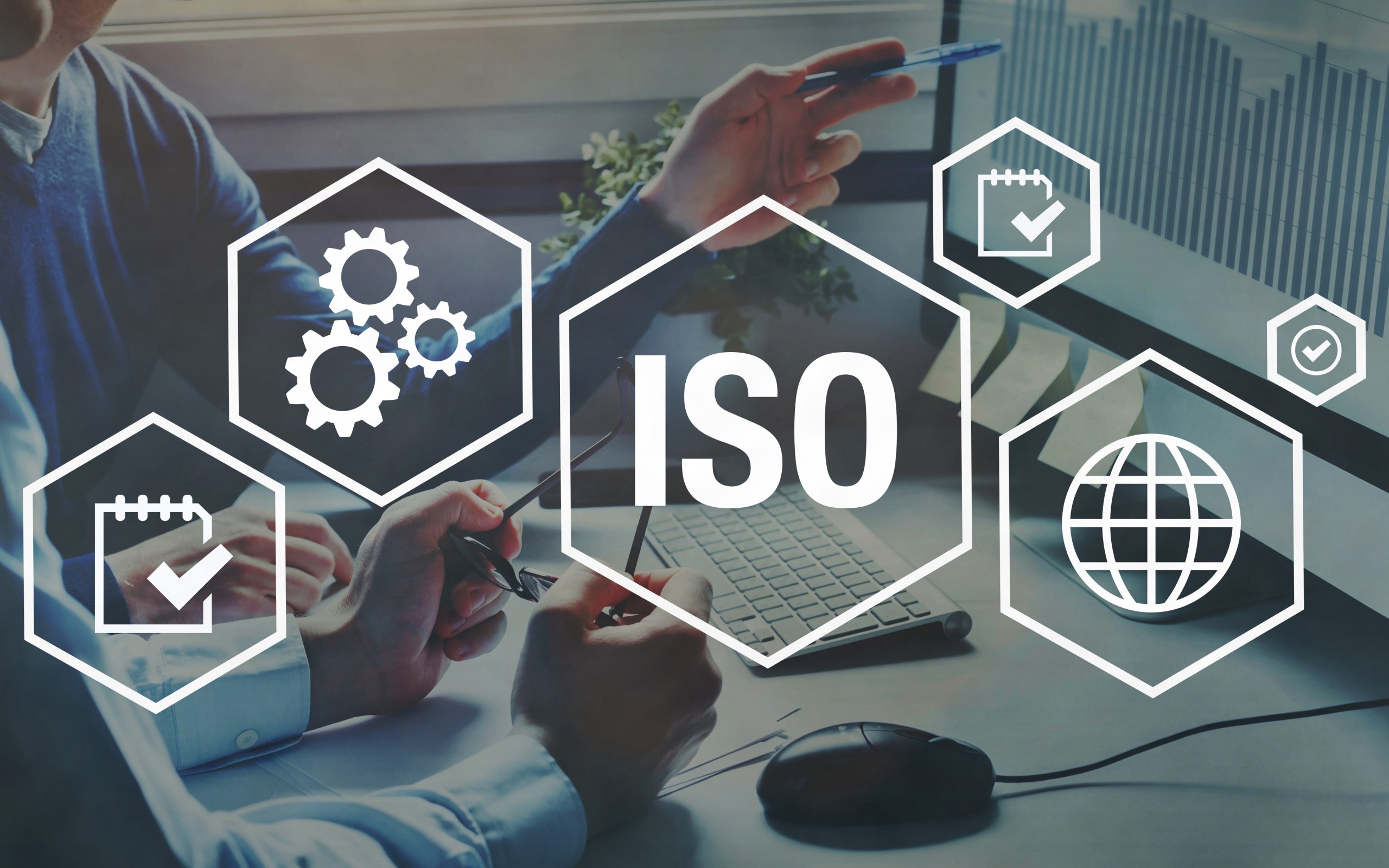
Mesures d'atténuation
Même si les mesures susmentionnées sont prises, il peut subsister des différences de couleur, de brillance et de rugosité qui ne peuvent être totalement éliminées au cours du processus de sablage. Dans ce cas, les entreprises peuvent envisager les mesures d'atténuation suivantes.
Technologie de correction des différences de couleur
Pour les pièces qui ont été sablées, la différence de couleur peut être corrigée par un revêtement ou un traitement de coloration ultérieur. L'application de revêtements et de techniques de teinture appropriés peut couvrir ou améliorer le problème de la différence de couleur dans une certaine mesure. Cela permet non seulement d'améliorer la qualité esthétique du produit, mais aussi de renforcer sa résistance à la corrosion et à l'usure, et de prolonger sa durée de vie.
Optimiser les paramètres du processus
En ajustant constamment les paramètres de sablage, les entreprises peuvent minimiser les différences de couleur et les incohérences. Par exemple, il faut affiner la pression, la vitesse et l'angle de la buse pendant le processus de sablage afin d'optimiser l'effet de sablage. Après avoir procédé à ces ajustements, les entreprises doivent effectuer des contrôles de qualité continus pour s'assurer que la qualité du produit final est conforme aux normes.
Inspections régulières
La mise en place d'un mécanisme strict d'inspection de la qualité permettra de détecter et de corriger rapidement les problèmes liés au processus de sablage. Les entreprises peuvent effectuer des contrôles de qualité à plusieurs niveaux avant, pendant et après le sablage pour s'assurer que chaque pièce est conforme aux normes de qualité spécifiées. Grâce à la surveillance en temps réel et à l'analyse des données, les entreprises peuvent rapidement identifier les problèmes potentiels et procéder aux ajustements et corrections nécessaires.
Lorsqu'elles sont confrontées à des problèmes tels que des différences de couleur, de brillance ou de rugosité dans le processus de sablage, les entreprises peuvent les surmonter et les atténuer grâce à diverses méthodes. Que ce soit par le contrôle des matériaux, la production standardisée, la modernisation des équipements ou la formation des employés, les entreprises peuvent améliorer la qualité des produits dans le cadre d'un processus d'optimisation continue. Même si ces problèmes ne peuvent être complètement éliminés, des mesures telles que la technologie de correction des différences de couleur, l'optimisation des paramètres du processus et la mise en place d'un mécanisme d'inspection régulier peuvent réduire efficacement les fluctuations de la qualité et garantir l'avantage du produit dans la concurrence du marché. Grâce à l'amélioration continue, les entreprises resteront compétitives dans l'environnement féroce du marché et gagneront la confiance et la satisfaction des clients.
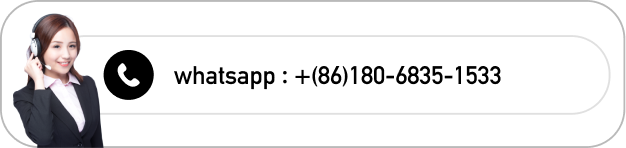