Cómo mejorar la vida útil de los muelles en la industria del automóvil
9 de septiembre de 2024
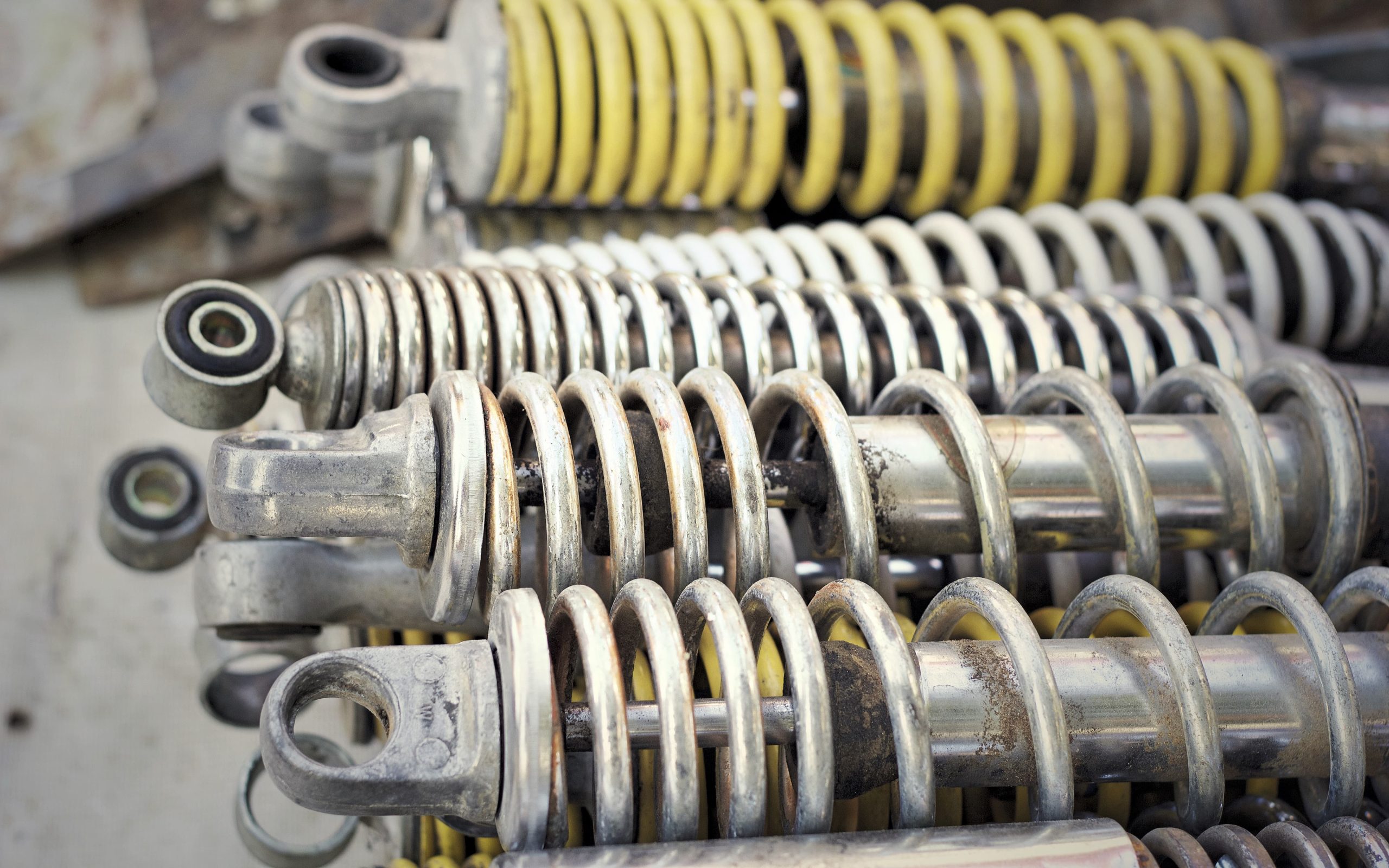
In automobile manufacturing, springs are one of the important components. They play a key role in components such as suspension systems, clutches, gearboxes, brake systems and seats. Therefore, the life and performance of springs will directly affect the safety and comfort of the vehicle. However, springs are subject to various stresses during use, such as cyclic loading, temperature changes and corrosion, leading to fatigue and wear. Therefore, how to extend the life of springs has become an important topic of concern for automobile manufacturers and material engineers, and shot peening technology has thus entered the field of vision. This technology greatly improves the fatigue resistance and durability of springs by introducing compressive residual stress, and ceramic peening beads have surpassed the rest of the shot peening materials with their superior performance and become the preferred choice.
Let me first introduce the common types of springs in the automotive industry and their applications:
- Coil springs
Coil springs are used in automotive suspension systems. By absorbing road bumps and vibrations, they ensure good stability and comfort during driving. Usually used in conjunction with shock absorbers, they are suitable for most ordinary cars and light trucks.
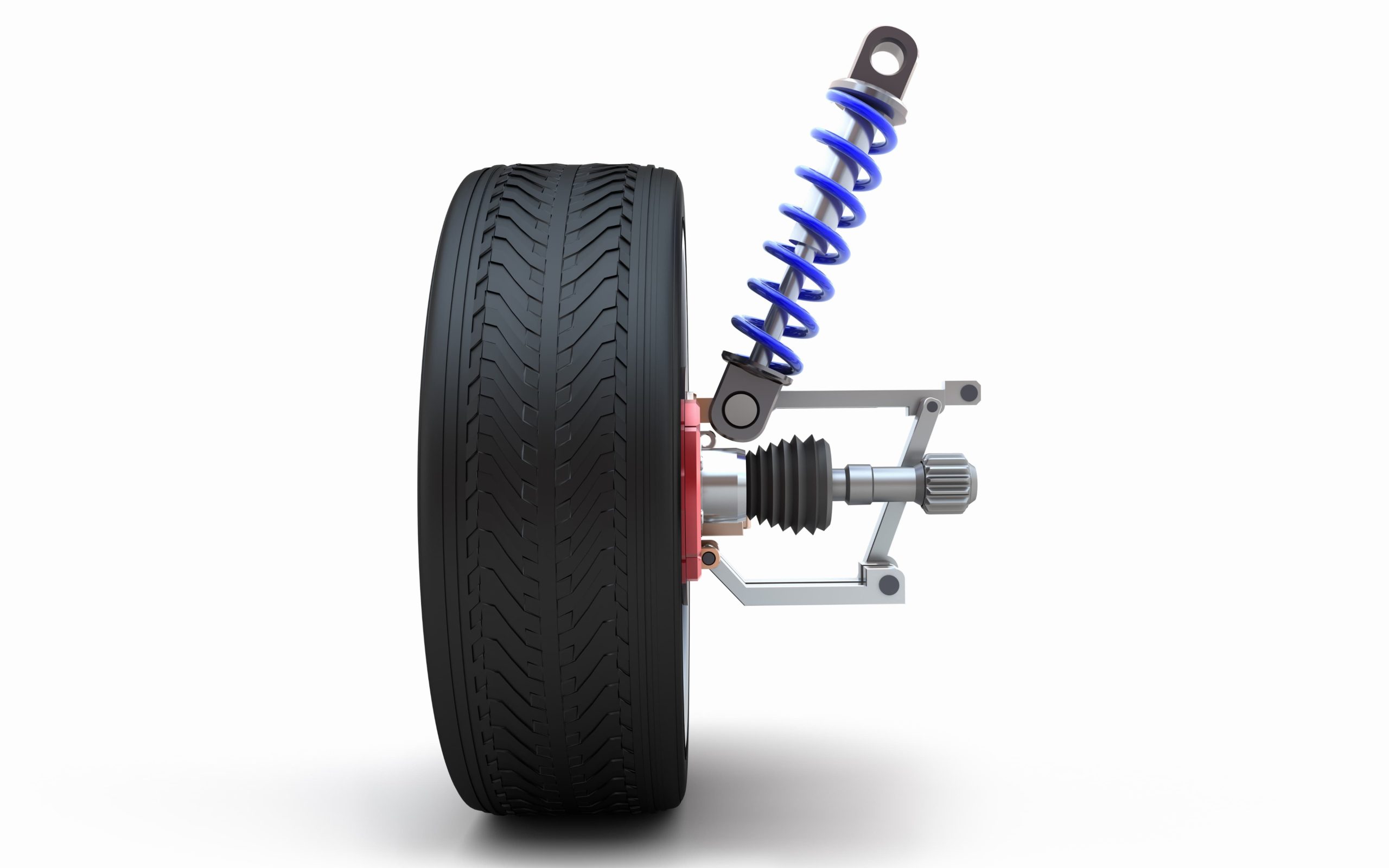
Coil spring with shock absorber
- Leaf springs
The leaf springs with a sturdy structure are mainly used in the rear suspension systems of trucks, SUVs and commercial vehicles. Made of multiple layers of thin steel plates, it has strong load capacity and durability (must be) and is often used on heavy vehicles.
- Air spring
Air spring uses compressed air as an elastic medium, which can adjust the suspension hardness according to the load and driving conditions to provide a comfortable driving experience. It is often used in the suspension systems of high-end cars and heavy trucks.
- Torsion bar spring
Absorbs and releases energy through the torsion bar to achieve the effect of a spring. It is usually used in the suspension systems of SUVs and trucks. Because it needs to adapt to harsh road conditions, it must have extremely strong durability.
- Valve spring
Used in the intake and exhaust valves of the engine to ensure that the valve can rebound quickly and remain closed at high speeds. It needs to have high strength and high temperature stability to ensure the normal operation of the engine at high speeds.
- Clutch spring
Used for the separation and combination of the clutch to ensure smooth power transmission. It must be able to withstand frequent operations and high temperature working environments to maintain stable performance.
- Brake spring
Applied to drum brake systems, it is used to pull the brake shoes back to their original position to ensure the reliability and safety of the brake system.
- Seat springs
Commonly used in seat backs and bases, they provide comfortable support and elasticity, and reduce the driver’s fatigue after long-term riding.
- Suspension airbag springs
As part of the air suspension system, airbag springs can automatically adjust the hardness of the suspension according to road conditions, providing excellent driving comfort and vehicle control, especially when overloaded or driving long distances. Therefore, they are often used in luxury cars, SUVs and trucks.
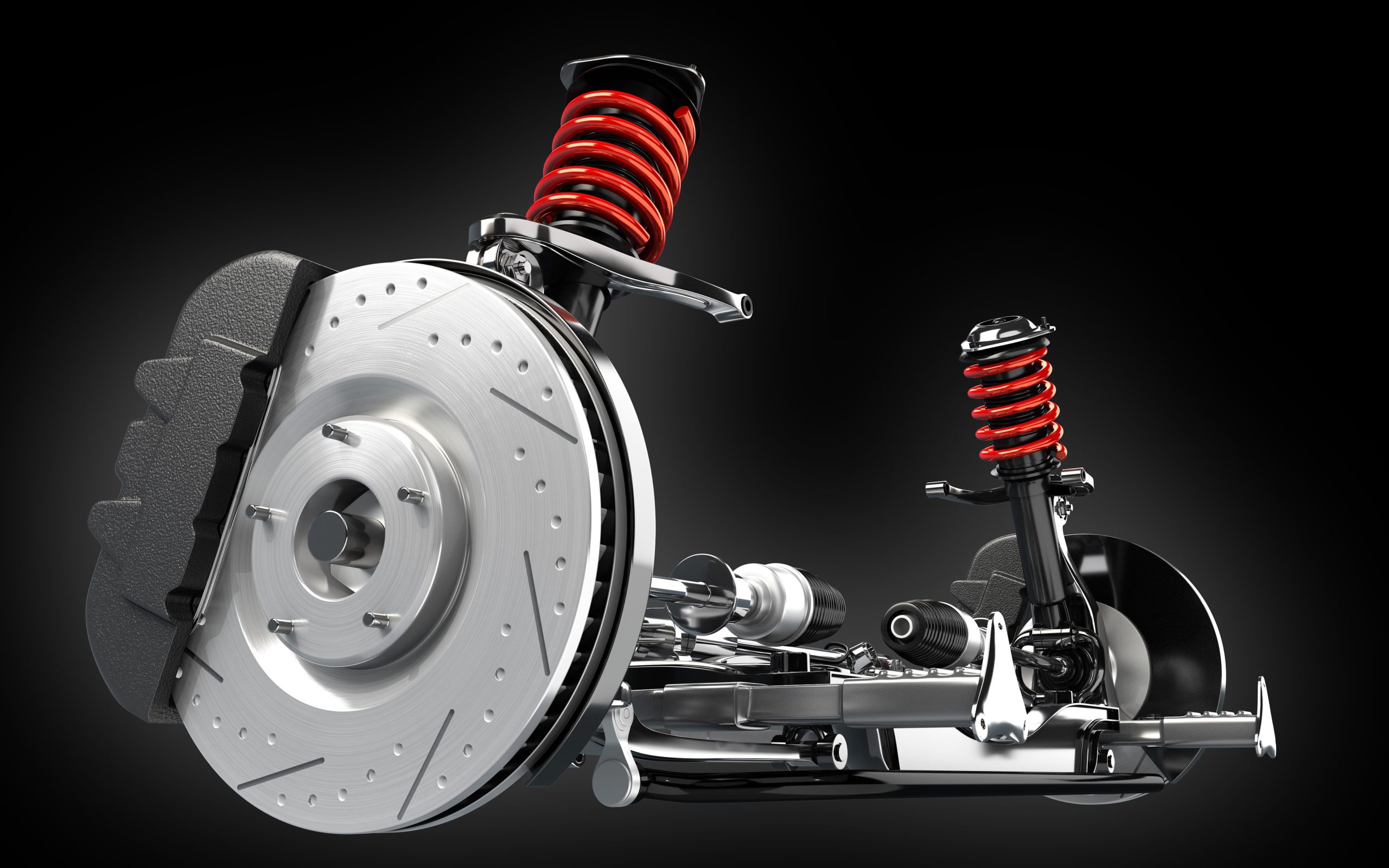
Automobile suspension spring
In summary, we have a general understanding of the types and functions of these springs. They are widely used in the automotive industry to meet the needs of different vehicle systems and applications. Their importance can be seen. However, due to stress relaxation, springs will undergo small permanent deformations when working under external forces for a long time, especially for springs working at high temperatures, where stress relaxation will be more serious. In addition, surface defects such as scratches, creases, oxidation and decarburization cannot be ignored. These are potential risks. Therefore, shot peening technology is needed to improve the surface quality and surface strength of the springs, so that the surface is in a compressive stress state, which can effectively improve the fatigue strength and service life of the springs.
In shot peening technology, why should ceramic peening beads be chosen as a medium? What are its advantages over traditional steel ball peening media? The following will answer your questions through four parts: surface damage after treatment, residual stress effect, roughness effect, and fatigue life comparison:
Surface damage after treatment
Ceramic peening beads have a higher hardness and can more effectively remove surface impurities and microcracks, but at the same time can reduce surface damage. However, the impact force of steel balls is too large, which can easily leave large pits on the surface, causing surface damage. In addition, the faster wear rate of steel balls may also cause contamination and affect surface quality.
According to Toyota’s research, when ceramic peening beads are used to treat engine parts, the surface damage is significantly lower than that of steel balls. This difference improves the overall quality of the parts and reduces the need for subsequent processing.
Residual stress effect
The high hardness (higher than glass beads and some steel balls) and low wear resistance of ceramic peening beads enable them to produce a deeper and more uniform compressive residual stress layer during the shot peening process, effectively improving the fatigue resistance of the spring. However, steel balls may produce large local stress concentrations during the shot peening process. Especially when dealing with high-strength materials, this uneven stress distribution may cause early failure of the material.
X-ray diffraction analysis shows that the surface residual stress of Z210 ceramic shot is higher than that of S230 steel shot. The average surface stress of Z210 shot peened spring is about -600~-650 MPa, while the normal surface stress of steel shot peening is -400 MPa, which is 50% higher. By adjusting the intensity of shot peening, the effect of shot peening on depth can be adjusted. We can conclude that surface residual stress and maximum stress at depth are very important when considering the fatigue performance of springs. 1
According to the test published by BMW, when the suspension springs are treated with ceramic peening beads, the residual stress distribution is more uniform and the fatigue resistance of the material is significantly improved.
Roughness effect
In the process of extending the life of the spring, surface roughness is an important factor affecting the growth of fatigue cracks. Since the surface of ceramic beads is relatively smooth, the surface roughness of the treated parts is low, which is suitable for applications that require precision surface treatment, such as the manufacture of other high-precision parts such as engine valve springs. However, steel balls may cause large surface roughness changes during shot peening due to their impact force and hardness, especially when dealing with irregular surfaces, which may affect the quality of the final product.
Generally, the surface roughness (Ra value) after ceramic peening treatment is between 0.2-0.4 μm, while the surface roughness after steel shot peening treatment may reach 0.8 μm or higher.
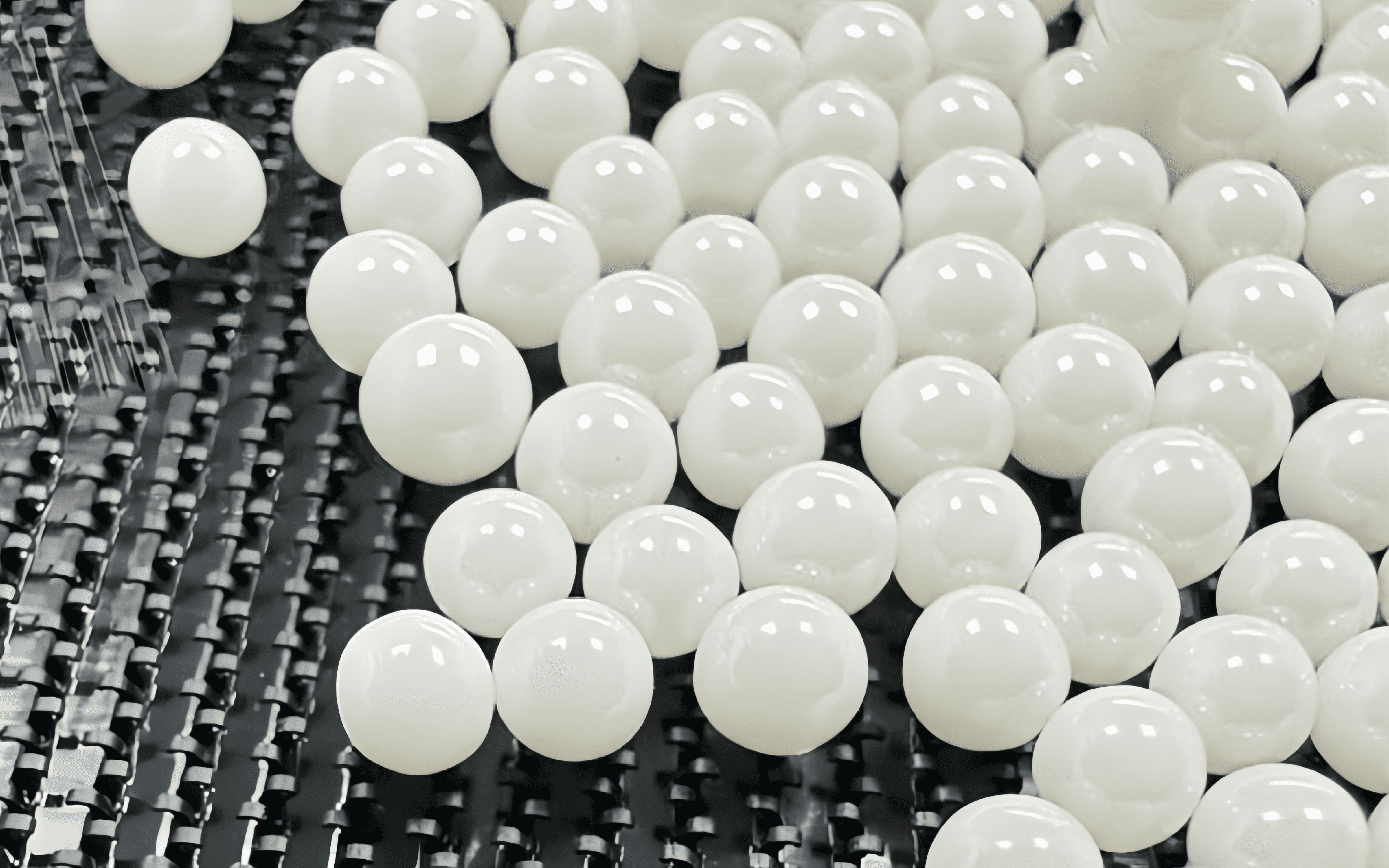
Smooth and round ceramic peening beads
Fatigue life comparison
Springs treated with ceramic peening beads have lower surface roughness and a lower probability of cracking. In addition, the compressive residual stress introduced by the ceramic beads can effectively offset the tensile stress during operation and prevent crack propagation, thereby significantly improving the fatigue life of the spring. In contrast, after steel ball treatment, the surface roughness is higher. Although there is a deeper compressive residual stress layer, it is easy to form stress concentration points on the surface, thus affecting fatigue performance.
Toyota’s test data shows that the fatigue life of suspension springs treated with ceramic peening beads increased by about 30%, while the treatment results with steel balls failed to achieve the same effect.
In order to improve the durability of the springs of its high-performance models, a well-known European automobile manufacturer decided to use ceramic peening beads to treat the springs. After standard fatigue testing, untreated springs cracked after about 50,000 cycles, but after treatment with ceramic shot peening beads, the fatigue life of the springs increased to about 80,000 cycles, an increase of 60%. This improvement significantly improves vehicle reliability and safety, while also reducing maintenance costs, successfully proving the effectiveness of ceramic peening beads in improving spring fatigue life. 2
In the United States, an automotive parts supplier has also implemented a similar ceramic shot peening bead treatment program. The supplier focuses on providing high-performance spring components to various automobile manufacturers. To optimize the durability of the springs, the company uses ceramic peening beads with a size of 150 microns (0.15 mm) for treatment. According to statistics, the average fatigue life of untreated springs in standard load tests is 40,000 cycles. In contrast, after treatment with ceramic peening beads, the fatigue life of the springs increased to 65,000 cycles, an increase of 62.5%. In addition, this process also helps the springs maintain good performance in high-stress environments, thereby improving the market competitiveness of the final product. 3
In an Asian automotive manufacturer, the application of ceramic peening beads has also shown excellent results. The company introduced ceramic peening beads with different particle sizes to meet the processing requirements of different types of springs. After testing, the springs began to show fatigue cracks in 100,000 load tests without shot peening. After treatment with ceramic peening beads, the fatigue life of the springs increased to 150,000 cycles, an increase of 50%. The introduction of this technology not only extended the service life of the springs, but also improved the performance of the overall product, giving the company a significant advantage in the market. 4
Through the above cases, we can see the significant effect of ceramic peening beads in various aspects, especially in enhancing the fatigue life of springs. These successful applications prove the great potential of ceramic peening beads in improving the performance and durability of automotive springs, but it should be noted that the size of springs used in the automotive industry is not consistent. Different types of springs have significant differences in shape, size, purpose and material. Their design is based on different load requirements, functions and installation space constraints. Therefore, the size required for shot peening will also vary depending on the specific size of the spring, the material and the required surface enhancement effect.
- Coil springs
The diameter, length and number of coils of coil springs depend on the requirements of the suspension system and are usually larger, with diameters ranging from a few millimeters to several centimeters. Therefore, the required shot size is usually 0.3-1.2 mm ceramic shot. This depends on the thickness of the spring and the target hardness. Larger shots are used to enhance surface hardness, while smaller shots are suitable for finer surface treatment.
- Leaf springs
Leaf springs are usually long strips of multi-layer steel plates with larger sizes and are often used in heavy-duty vehicles. Generally, 0.5-1.5 mm shots are selected. Since leaf springs are thicker and require stronger impact forces, larger shots may be used to enhance the fatigue resistance of the spring.
- Air springs
Air springs are mainly composed of rubber and steel and are larger overall, but shot peening is not always required because their core is made of rubber material. If shot peening of steel parts is involved, 0.4-0.8 mm shots can be used to ensure surface reinforcement of steel parts.
- Torsion bar springs
Torsion bar springs are straight bars with varying lengths and diameters. They are usually thinner than coil springs. Shots of 0.4-1.0 mm are usually selected. Depending on the diameter of the torsion bar, smaller torsion bars can use finer shots, while larger torsion bars require larger shots for surface treatment.
- Valve springs
Valve springs are smaller in size, with diameters usually ranging from a few millimeters to a few centimeters. Since valve springs are delicate and have high requirements for surface finish, smaller shots are usually used for surface strengthening. Shot sizes of 0.2-0.6 mm are more suitable.
- Clutch springs
Clutch springs are usually medium in size and small in diameter, but the length and shape will vary. Since clutch springs work in a high-stress environment, the goal of shot peening is to enhance their fatigue strength, so medium-sized shots of 0.3-0.8 mm are selected.
- Brake springs
Brake springs are smaller, usually only a few millimeters to a centimeter in diameter. Smaller shot peening is used for precision small brake springs to maintain their accuracy and surface quality, 0.1-0.4 mm shot peening is best.
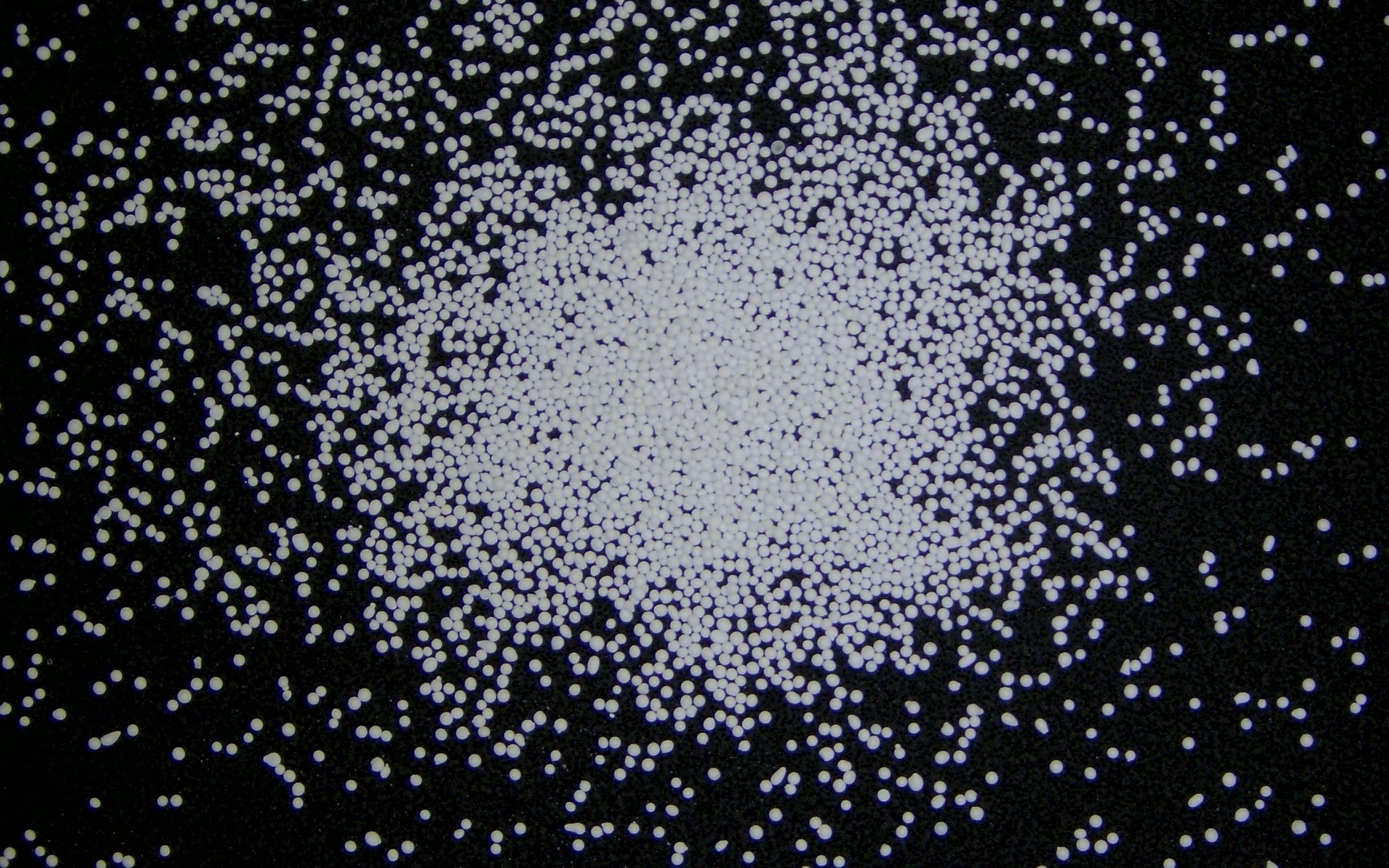
Shot peening for precision workpieces
- Seat springs
Seat springs are usually slender and small in diameter, similar to valve springs. To improve the durability and fatigue resistance of the springs, use 0.2-0.5 mm shot peening.
- Suspension airbag springs
Suspension airbag springs have larger steel components and are usually of various sizes. Depending on the size of the suspension steel parts, choose larger 0.5-1.0 mm shot peening for surface strengthening and extending its service life.
In summary, since different types of springs have different design requirements and use environments, it is crucial to choose the right shot peening bead size. Whether it is a coil spring, leaf spring or a smaller valve spring, shot peening for the special requirements of different springs can achieve the best surface strengthening effect. You can choose the specific shot peening for your spring according to the size table in our product details, and we can also customize the size according to your requirements!
When exploring how to improve the life of springs in the automotive industry, we are not just talking about technical improvements, but also focusing on how to bring a better driving experience through technological innovation. As the “invisible hero” of the car, the spring silently bears the challenges of the vehicle under various working conditions. The introduction of ceramic shot peening technology is precisely to make these “invisible heroes” more durable and more reliable. From coil springs to air springs, the optimization of each spring means less maintenance, longer service life, and higher safety. When you know that your car springs have undergone the most advanced treatment and can withstand various challenges, your confidence and sense of security will be greatly enhanced. This enhanced driving experience and sense of security are the ultimate goals pursued by any technological innovation.
The widespread application of ceramic shot peening technology allows us to see how a technology has come from behind the scenes to the front stage and become the key to improving product quality and user experience. It not only promotes the development of the automotive industry, but also further demonstrates how technology can play an important role in subtle places. In the future, with the continuous innovation and application of more technologies, we can expect the automotive industry to bring more surprising progress and changes.
Referencias
- APPLICATION OF CERAMIC SHOT FOR PEENING OFAUTOMOTIVE SUSPENSION COIL SPRINGS
- Case Study: Ceramic Shot Peening in Automotive Springs – European Manufacturer
- U.S. Automotive Supplier: Performance Improvement with Ceramic Shot Peening
- Asian Automotive Manufacturer: Innovations in Shot Peening
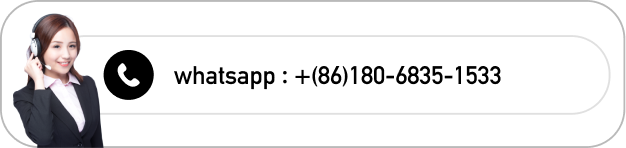