Циркониевые бусины в сравнении со стеклянными бусинами
22 января 2025 г.
In industrial surface treatment and grinding processes, yttria-stabilized zirconia beads and glass beads are two common media. They both have functions such as cleaning, deburring and strengthening, but in actual applications, zirconia beads are gradually replacing glass beads with their excellent physical and mechanical properties and becoming the preferred medium in many fields.
Applicable material range
Applicable materials for zirconia beads
Yttria-stabilized zirconia beads can handle a variety of materials with their high hardness, high density, and chemical stability, especially on workpieces with high hardness or extremely high surface quality requirements:
1. High-hardness metals:
- Stainless steel: Remove oxide layers, stains, or burrs from the surface, while achieving a matte effect without affecting the strength and finish of the workpiece.
- Titanium alloy: Precisely strengthen titanium alloy parts used in aerospace to improve fatigue resistance and durability.
2. Ceramics: Zirconia beads are suitable for finishing ceramic products to improve surface smoothness and wear resistance. They are also used in electronic components and medical devices.
3. Композитные материалы: Used for surface strengthening and cleaning composite materials in aerospace to avoid debris contamination.
4. High-strength, high-performance plastic parts (such as carbon fiber-reinforced plastics)
Applicable materials for glass beads
Due to the limitations of their physical properties, glass beads are not suitable for surface treatment of high-hardness workpieces:
- Aluminum and aluminum alloys: Glass beads perform well in cleaning oxide layers and coatings, but cannot penetrate deep into the surface to strengthen the surface.
- Copper and brass: Glass beads can decontaminate and polish these metals without damaging the gloss of the workpiece.
- Soft plastics: Glass beads can complete surface decoration without damaging the surface of soft plastics, but their cleaning efficiency is not as good as zirconia beads.
Comparison of sandblasting effects
Advantages of zirconia beads
- Higher hardness
Zirconium oxide beads have a Mohs hardness of up to 9, which can easily remove stubborn dirt and surface contaminants compared to 6-7 glass beads. Especially when dealing with high-hardness metals, zirconia beads can provide a more thorough and uniform cleaning effect.
- Consistent gloss and texture
Zirconium oxide beads have a smooth, shiny surface, which is very critical in the sandblasting process. Because the smoother the surface of the medium, the more uniform the friction with the workpiece, and the less wear is generated. Therefore, zirconia beads can achieve a more delicate and smooth texture effect on the surface of the workpiece, reducing roughness and defects. In addition, the smooth spherical surface can also reflect a better mirror effect after sandblasting, while the rougher spherical surface will cause uneven surface reflection, affecting the overall appearance quality.
For example, the figure below shows the effect of 80-mesh glass sandblasting on the left and the effect of zirconia beads blasting on the right. The two colors are different. The glass sand is dark and has no luster. The color of zirconium oxide beads is bright, which is silver-white – the original base color of the steel plate.
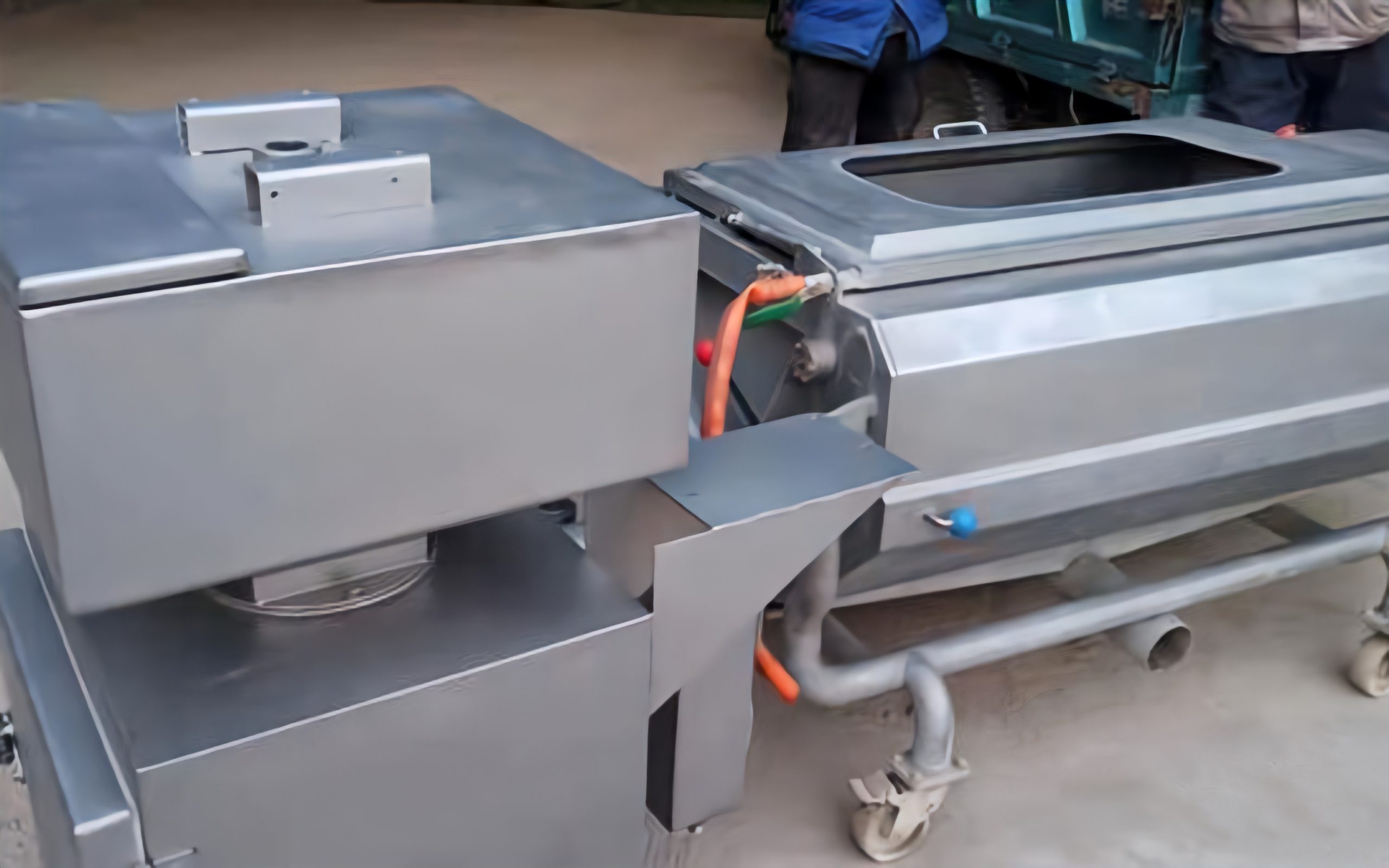
- Higher durability
Zirconium oxide beads are not easy to break during impact due to their excellent fracture resistance, and can be recycled many times even in high-intensity sandblasting processes. This not only ensures the consistency of the sandblasting effect, but also significantly reduces the frequency of medium replacement and reduces production costs.
Disadvantages of glass beads
- Physical reasons for fragility
The brittleness of glass beads comes from their internal amorphous structure. Glass materials lack the slip plane in the crystal structure. When impacted by external forces, they cannot effectively disperse stress, and are prone to breakage under high-energy impact, which in turn damages the surface of the workpiece. In contrast, the dense crystal structure of zirconium oxide beads enables them to better absorb and disperse external forces to avoid breakage.
- Insufficient hardness and durability
Glass beads have low hardness and cannot effectively process high-hardness metal surfaces. In addition, due to the rapid wear of the particle shape and size during use, the surface texture after sandblasting is not uniform and is prone to leaving visible marks.
Grinding efficiency comparison
Advantages of zirconia beads
- High energy transfer efficiency
The density of zirconium oxide beads is as high as 6 g/cm³, which is more than twice that of glass beads (2.4-2.6 g/cm³). During the grinding process, the impact energy per unit volume is higher, and high-intensity deburring and surface finishing tasks can be completed in a short time.
- Long service life
Zirconium oxide beads are mainly composed of zirconium oxide and yttrium oxide, with good fracture toughness, high elastic modulus, linear expansion coefficient similar to that of metal, and excellent wear resistance, which is about 20 times that of glass beads. This means that in the continuous grinding process, zirconia beads can not only maintain efficient grinding but also will not break, greatly reducing the frequency of media replacement and improving production efficiency.
- Adaptability to high-viscosity and hard materials
When dealing with high viscosity or high hardness materials (such as ceramic powders or electronic slurries), the stability and durability of zirconium oxide beads make them particularly outstanding. Glass beads often fail due to cracking or excessive surface wear under similar conditions.
Disadvantages of glass beads
- Low grinding efficiency
Due to their low density, the impact force provided by glass beads during the grinding process is insufficient, making it difficult to meet industrial needs that require high processing efficiency.
- Fragility leads to higher replacement frequency
The fragility of glass beads not only reduces the consistency of the grinding effect, but also requires frequent replacement, increasing maintenance costs and downtime.
Overall, yttria-stabilized zirconia beads are superior to glass beads in terms of sandblasting effect and grinding efficiency due to their wider range of applications, high hardness, smooth surface, high density, and durability. Its excellent surface treatment ability and economic benefits make it an ideal choice to replace glass beads, especially in industrial applications with high-quality requirements, such as stainless steel surface strengthening, precision parts cleaning, and deburring of high-hardness materials.
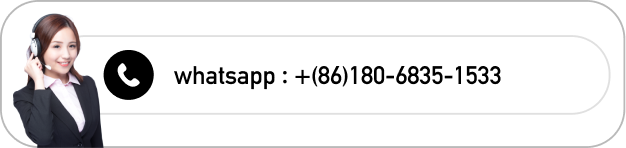