Сравнение керамических шариков и стальных дробин в компонентах турбины
4 января 2025 года

К компонентам турбин, являющимся ключевым компонентом в аэрокосмической и энергетической отраслях, предъявляются чрезвычайно высокие требования по производительности и надежности. Дробеструйное упрочнение является важным техническим средством оптимизации поверхности деталей турбин путем введения остаточных сжимающих напряжений для повышения усталостной прочности и коррозионной стойкости материалов.
Керамические дробеметные шарики и стальные шарики - два наиболее часто используемых средства упрочнения. Хотя и те, и другие могут обеспечить определенный эффект упрочнения, существуют значительные различия в производительности, долговечности и стоимости. В этой статье мы рассмотрим эти различия, чтобы помочь пользователям лучше выбрать подходящие средства упрочнения.
Керамические шарики и стальная дробь
Керамические шарики для упрочнения являются разновидностью средств упрочнения, изготовленных из высокочистых керамических материалов, и обычно имеют белый или светло-серый цвет. Они обладают высокой твердостью, обычно в пределах 9,0 по Моосу, и подходят для тонкой обработки поверхности. Форма, как правило, сферическая или почти сферическая, с высокой однородностью и консистенцией. Плотность обычно составляет 2,5-3,0 г/см³. По сравнению с металлическими материалами для упрочнения, его легкие характеристики помогают уменьшить воздействие на подложку и улучшить качество и эффект обработки поверхности.
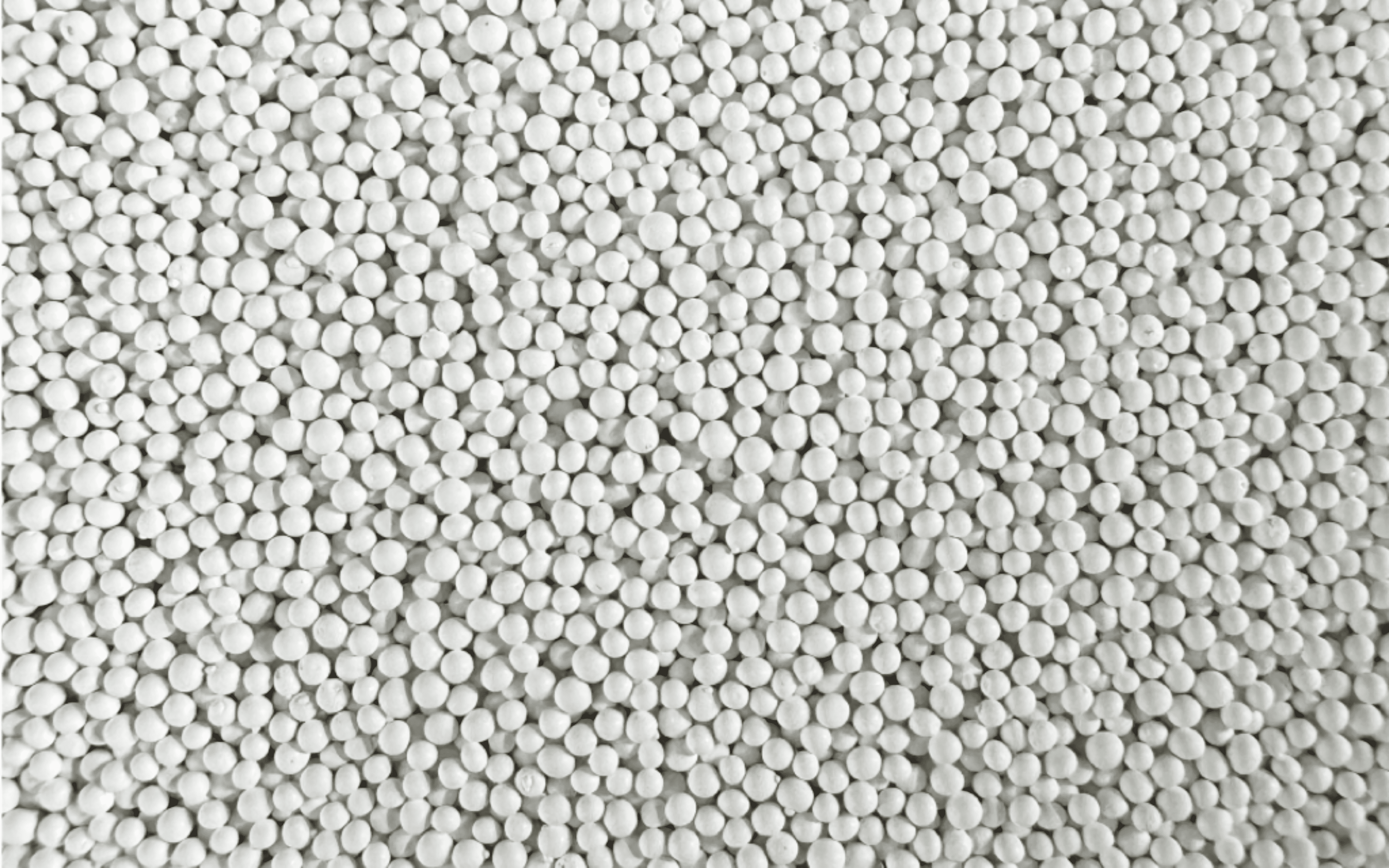
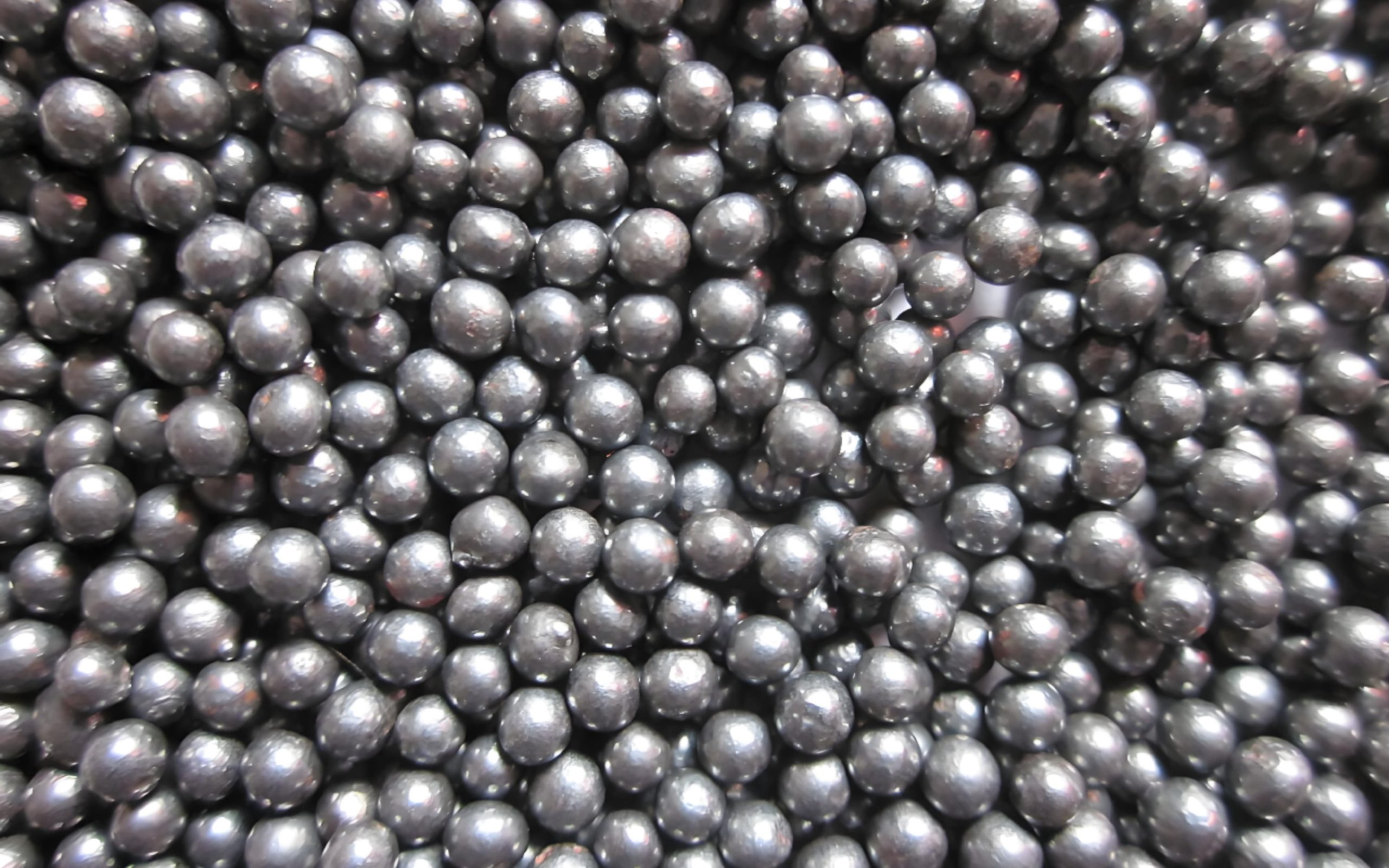
Стальная дробь это средство для упрочнения, изготовленное из высокоуглеродистой стали, обычно серого металлического цвета, с высокой твердостью около 45-55 HRC (твердость по Роквеллу, ниже, чем у керамической дроби). Стальная дробь обычно сферическая или почти сферическая, с высокой плотностью, обычно 7,5-8,0 г/см³. Благодаря своей твердости она подходит для обработки поверхностей деталей, подвергающихся большим ударным нагрузкам. Он может эффективно удалять оксидный налет и загрязнения, а также укреплять поверхность. Он хорошо подходит для обработки шероховатых поверхностей и дробеструйного упрочнения с большой нагрузкой.
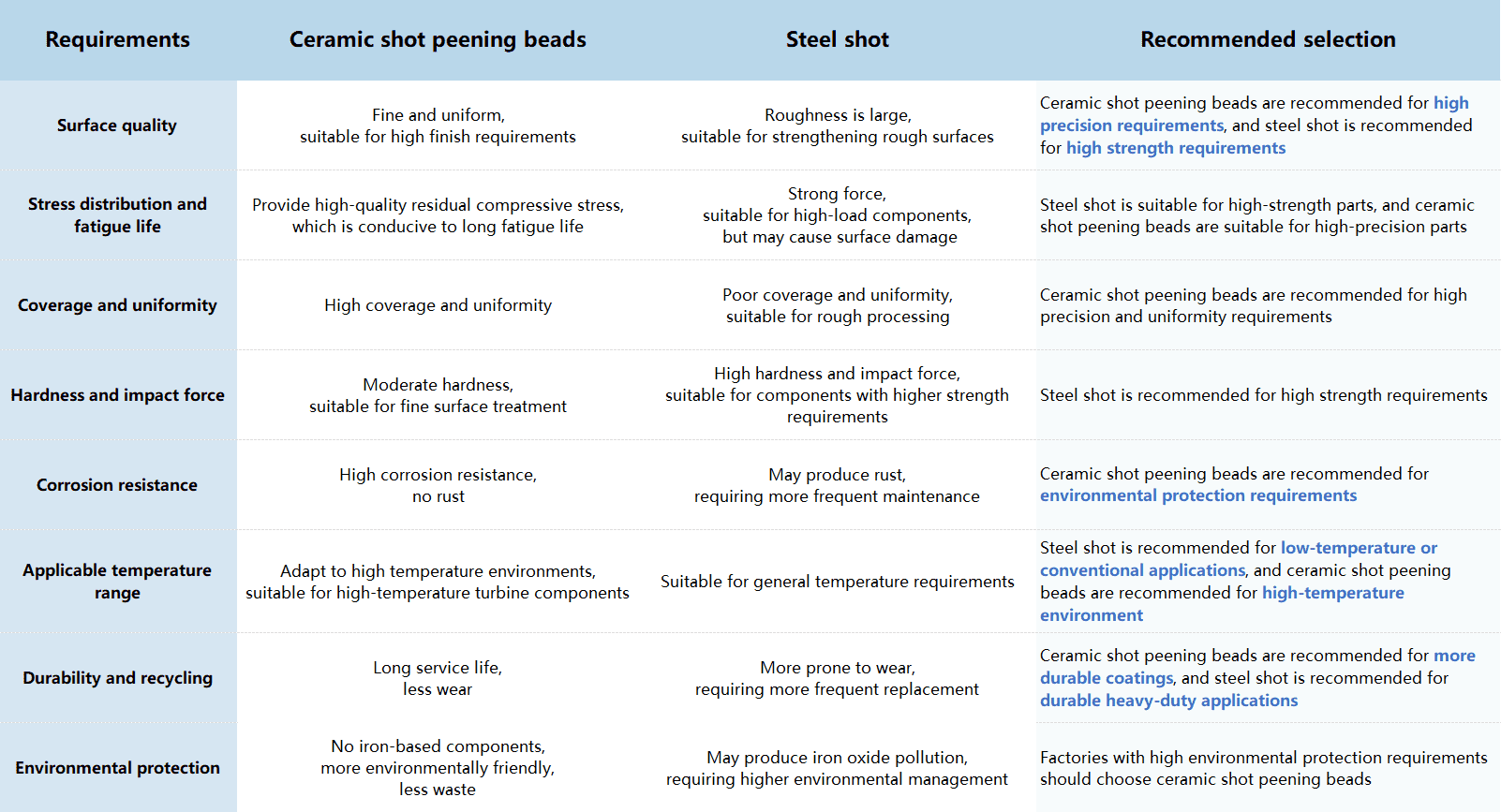
Сравнение эффектов дробеструйного упрочнения деталей турбин
- Шероховатость поверхности
Несмотря на то, что керамические шарики для упрочнения обладают высокой твердостью, они не повреждают поверхность и позволяют получить низкую шероховатость поверхности при сохранении эффективности обработки. Обычно они подходят для деталей турбин с высокими требованиями к чистоте поверхности, таких как лопатки турбин авиационных двигателей.
Несмотря на сильную ударную силу, он легко создает высокую шероховатость и не подходит для деталей турбин, требующих деликатной обработки поверхности.
- Отделка поверхности
Поверхность циркониевой керамической дроби гладкая, на ней нелегко образуются царапины или вмятины после удара, что позволяет достичь равномерного эффекта обработки поверхности.
Стальная дробь обычно изготавливается из высокоуглеродистой или легированной стали. Хотя сталь обладает высокой твердостью, структура ее частиц относительно хрупкая. Она легко деформируется или разрушается при высокой интенсивности или частом использовании, что может привести к неравномерному ударному эффекту и, таким образом, повлиять на общее качество обработки.
- Распределение напряжений
Керамические шарики имеют однородный размер и могут создавать равномерную и умеренную глубину остаточного сжимающего напряжения в поверхностном слое, что способствует повышению усталостной долговечности. Глубина распределения сжимающего напряжения обычно достигает 0.1-0.15 мм, что является предпочтительным выбором для деталей, чувствительных к нагрузкам.
Стальная дробь может создавать более глубокое распределение остаточных сжимающих напряжений (глубина может достигать более 0,2 мм) за счет более высокой силы удара, но равномерность распределения напряжений может быть не такой хорошей, как у керамических шарошек, что оказывает определенное влияние на срок службы деталей.
- Покрытие
Керамические шарики имеют высокую консистенцию по размеру и форме, и процесс упрочнения может легко достичь более высокого покрытия, а эффективность покрытия обычно 10%-15% выше, чем у стальной дроби.
Стальная дробь склонна к недостаточному локальному покрытию из-за различий в форме и твердости, и для удовлетворения требований может потребоваться дополнительное время или многократное упрочнение.
- Равномерность
Керамические средства упрочнения состоят в основном из оксида циркония (на долю которого приходится 60%-70%), в сочетании с другими оксидами. Уникальная кристаллическая структура обладает превосходной прочностью на сжатие и вязкостью, нелегко разрушается и особенно подходит для работы в условиях высокой интенсивности и многократных ударов. Она позволяет поддерживать постоянный ударный эффект в процессе упрочнения и улучшает равномерность обработки.
Однако скорость разрушения стальной дроби выше, и после дробеструйного упрочнения могут образовываться частицы разного размера, что влияет на стабильность процесса дробеструйного упрочнения.
Сравнение производительности
- Устойчивость к коррозии
Керамические шарики для упрочнения обладают отличной коррозионной стойкостью и не подвержены воздействию влаги и химикатов. Они подходят для деталей, длительное время подвергающихся воздействию коррозионной среды. Например, в морских условиях или в условиях повышенной влажности дробь из циркониевой керамики может эффективно защитить целостность поверхности деталей турбин.
Стальная дробь легко поддается воздействию влаги и химикатов. При длительном использовании может появиться ржавчина, что ухудшает качество поверхности деталей турбины. Требуется дополнительная антикоррозийная обработка, что увеличивает стоимость и сложность использования.
- Диапазон применяемых температур
Керамические материалы обладают высокой термостойкостью и обычно сохраняют стабильную структуру в высокотемпературных средах. При этом не происходит размягчения материала или изменения формы. Они подходят для высокотемпературных деталей, таких как лопатки турбин авиационных двигателей.
Стальная дробь может выйти из строя из-за окисления или ухудшения характеристик в условиях сверхвысоких температур и не подходит для операций дробеструйного упрочнения при экстремально высоких температурах.
Долговечность и стоимость
- Долговечность
Керамические шарошки обладают высокой износостойкостью и гораздо большим сроком службы, чем стальная дробь. Исследования показали, что при одинаковых условиях керамические шарошки можно использовать в 2-3 раза чаще, чем стальную дробь.
По структурным причинам стальная дробь при высокочастотном использовании с большей вероятностью растрескается, что приведет к поломке, а срок ее службы значительно ниже, чем у керамических шарошек для упрочнения.
- Уровень переработки
Керамические шарики обладают высокой степенью рециркуляции и могут быть использованы повторно после простой очистки. Уровень потерь низкий, что помогает снизить расход материала при дробеструйном упрочнении в целом.
Степень переработки стальной дроби ниже, чем у дроби из циркониевой керамики. Из-за растрескивания и деформации она имеет большие потери и требует более частой замены и обработки, что повышает сложность и стоимость обслуживания.
- Экономика
Удельная стоимость циркониевой керамической дроби выше, но ее долговечность и высокая степень переработки делают ее более экономичной для долгосрочного использования. Стальная дробь имеет низкую первоначальную стоимость приобретения и подходит для проектов с ограниченным бюджетом или краткосрочных проектов. Больше внимания следует уделять высокоинтенсивным операциям дробеструйного упрочнения.
Сравнение сценариев применения
- Требования к высокой точности
Керамические шарики для дробеструйного упрочнения хорошо подходят для обработки высокоточных деталей, таких как лопатки турбин и детали авиационных двигателей. Обладая умеренной твердостью и равномерным размером частиц, они обеспечивают высококачественное упрочнение поверхности без ее повреждения.
Особенно для деталей со сложными деталями и высокими требованиями к качеству поверхности, таких как канавки и кромки лопаток турбин, эти детали обычно требуют тонкого контроля силы удара и равномерности среды упрочнения.
- Требования к высокой прочности
Стальная дробь имеет значительные преимущества в деталях, требующих высокоинтенсивного упрочнения, таких как крупные подшипники турбин и детали, работающие под давлением, благодаря своей большой силе удара.
Подходит для поверхностного упрочнения толстых и тяжелых металлических деталей, позволяет быстро достичь глубокого остаточного сжимающего напряжения, тем самым увеличивая усталостную долговечность деталей.
- Требования к охране окружающей среды
Керамические бусины не содержат компонентов на основе железа, производят меньше пыли и загрязняющих веществ и соответствуют стандартам защиты окружающей среды. Отходы, образующиеся в процессе использования, также относительно невелики, что позволяет сократить расходы завода на управление охраной окружающей среды.
Стальная дробь после износа может образовывать частицы оксида железа, что требует строгого контроля за состоянием окружающей среды. Частая замена также увеличивает объем утилизации отходов, что не подходит для производственных условий, в которых особое внимание уделяется экологичности производства.
Керамические и стальные дробеметные шарики имеют уникальные преимущества и подходят для различных задач дробеметного упрочнения деталей турбин.
Керамические шарики отлично подходят для обработки поверхностей лопаток турбин и сложных деталей с высокими требованиями к точности и обеспечивают равномерное и детальное упрочнение поверхности, что подходит для применений, требующих высокого качества поверхности и длительного срока службы. Стальная дробь, с другой стороны, демонстрирует непревзойденные преимущества, обеспечивая большую силу удара при обработке деталей, требующих глубокого сжатия, таких как крупные турбинные подшипники и детали, работающие под давлением.
Обе среды имеют свои особенности, и выбор должен основываться на конкретных требованиях к производительности, экологическим требованиям и экономическому бюджету компонентов турбины.
Благодаря постоянному совершенствованию технологий и материалов дробеструйного упрочнения в будущем могут появиться более инновационные средства упрочнения, обеспечивающие более точные и экологически безопасные решения для эффективной обработки компонентов турбин.
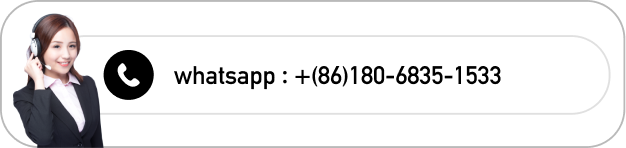