Отделка пресс-форм: общие проблемы и решения для отделки поверхности
17 января 2025 года
Surface finish is one of the most important considerations in mold finishing. It not only affects the beauty and functionality of the parts, but also directly determines the service life of the mold and product quality. From medical devices to automotive parts, different industries have different surface requirements for molds. Mold materials, tolerances, textures, demolding performance, material flow characteristics, and processing methods will affect the final finish effect. This article will focus on the surface finish problem of mold finishing, analyze its causes and provide solutions to help mold manufacturers cope with complex processing challenges.
Common problems with mold surface finish
Uneven surface roughness
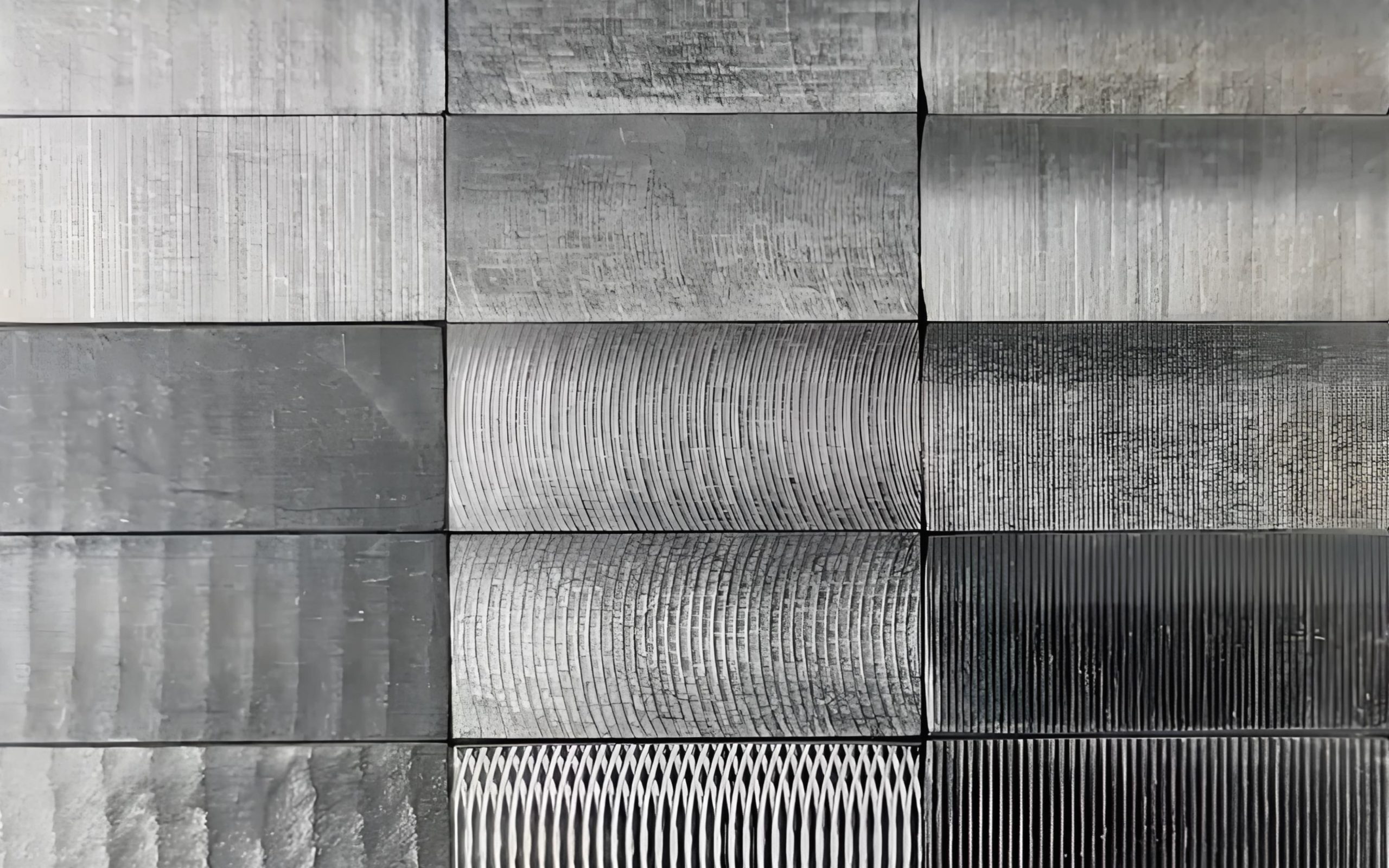
Problem manifestation
- The roughness of different areas on the mold surface is significantly different, affecting product consistency.
- The high light area and edge position are prone to excessive roughness.
- Significant knife marks appear on the surface after CNC processing, affecting the finish and visual effect.
- The texture of some areas is different in depth, affecting the subsequent polishing effect.
Cause analysis
- Insufficient machining accuracy and failure to optimize complex areas.
- The tool wear is not replaced in time, affecting the surface quality.
- Improper process parameter setting, unreasonable matching of feed speed and rotation speed, resulting in surface texture differences.
- Imperfect surface treatment process, improper medium selection in polishing and sandblasting steps.
Surface defects lead to demolding difficulties
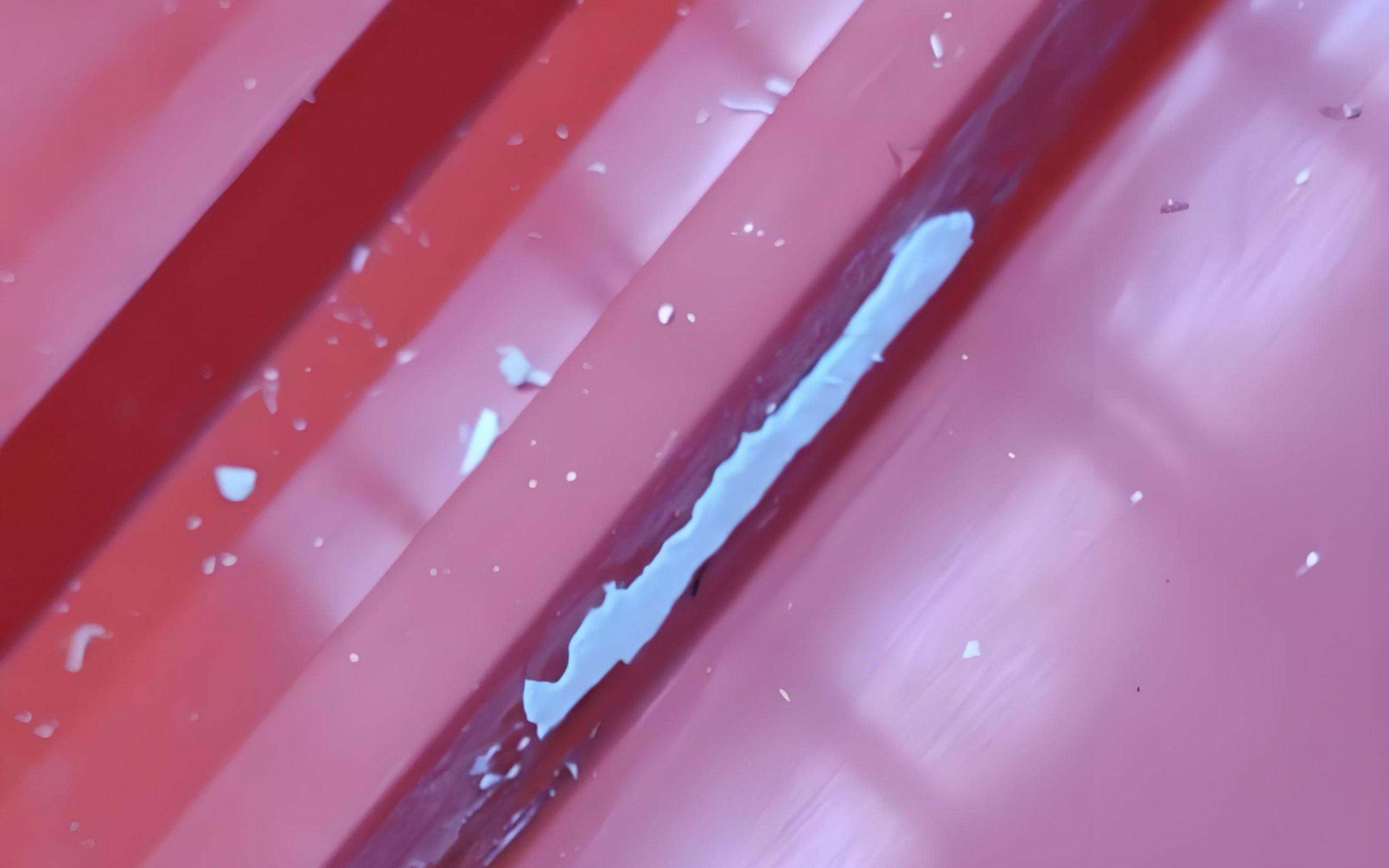
Problem manifestation
- The material adheres to the mold surface during demolding, affecting production efficiency.
- Some thermoplastics or silicones produce drawing or residual marks after demolding.
Cause analysis
- Insufficient finish and rough surface increase the adhesion of materials in the mold cavity.
- Unreasonable design of demolding angle, and failure to fully consider the demolding requirements of complex geometric shapes.
- Lack of surface texture, especially for sticky materials such as silicone, smooth surface may increase demolding difficulties.
Surface cracks and bubble problems
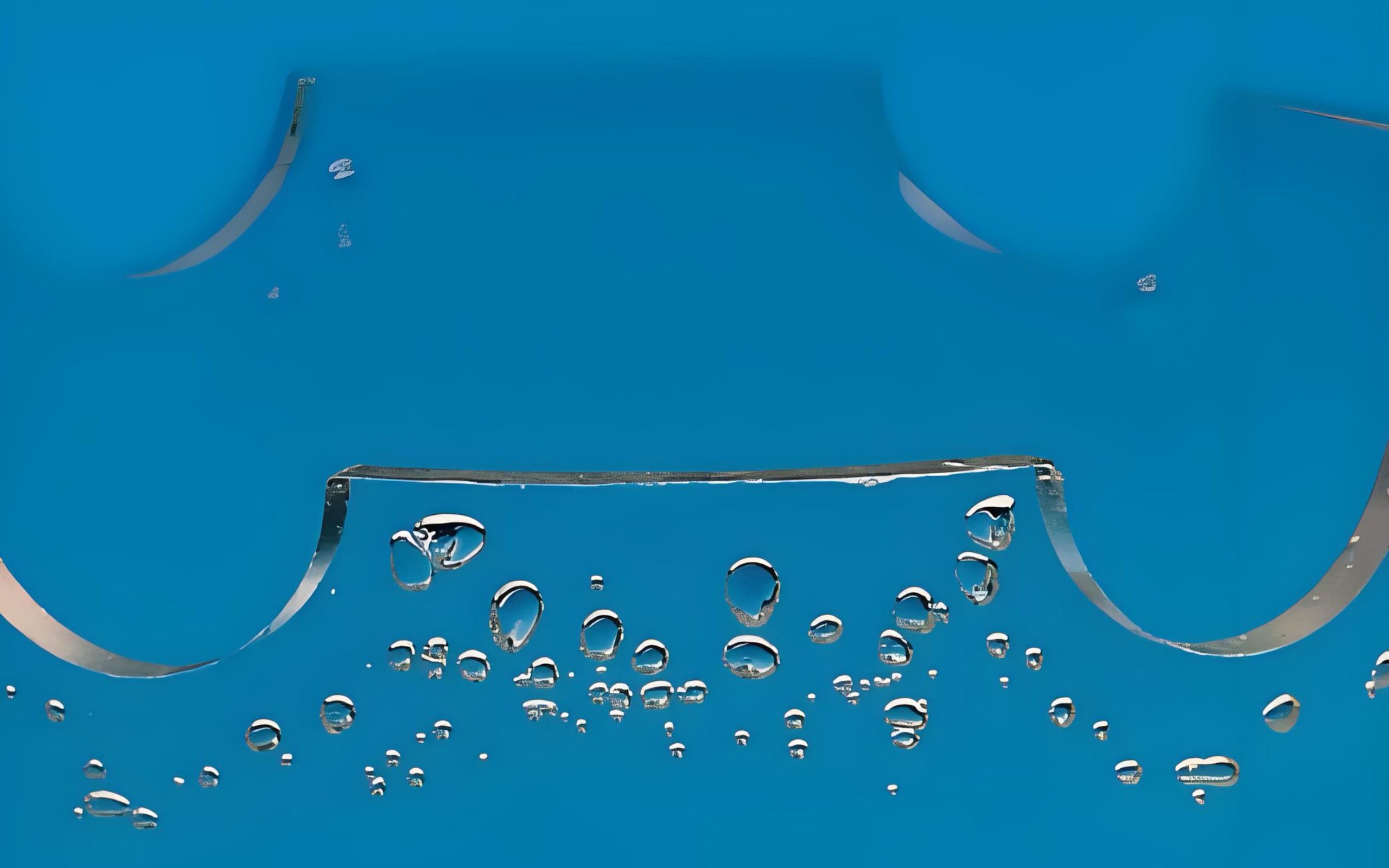
Problem manifestation
- Silver scratches or specks appear on the surface of the part, affecting the appearance and strength.
- Crack extension may cause the part to fail in application.
Cause analysis
- The water content of the injection molding material is too high, and bubbles are generated during cooling.
- The mold vent design is unreasonable, and the gas cannot be discharged from the mold cavity smoothly, resulting in crack formation.
- No effective crack repair and strengthening treatment after processing.
Surface impurities affect processing results
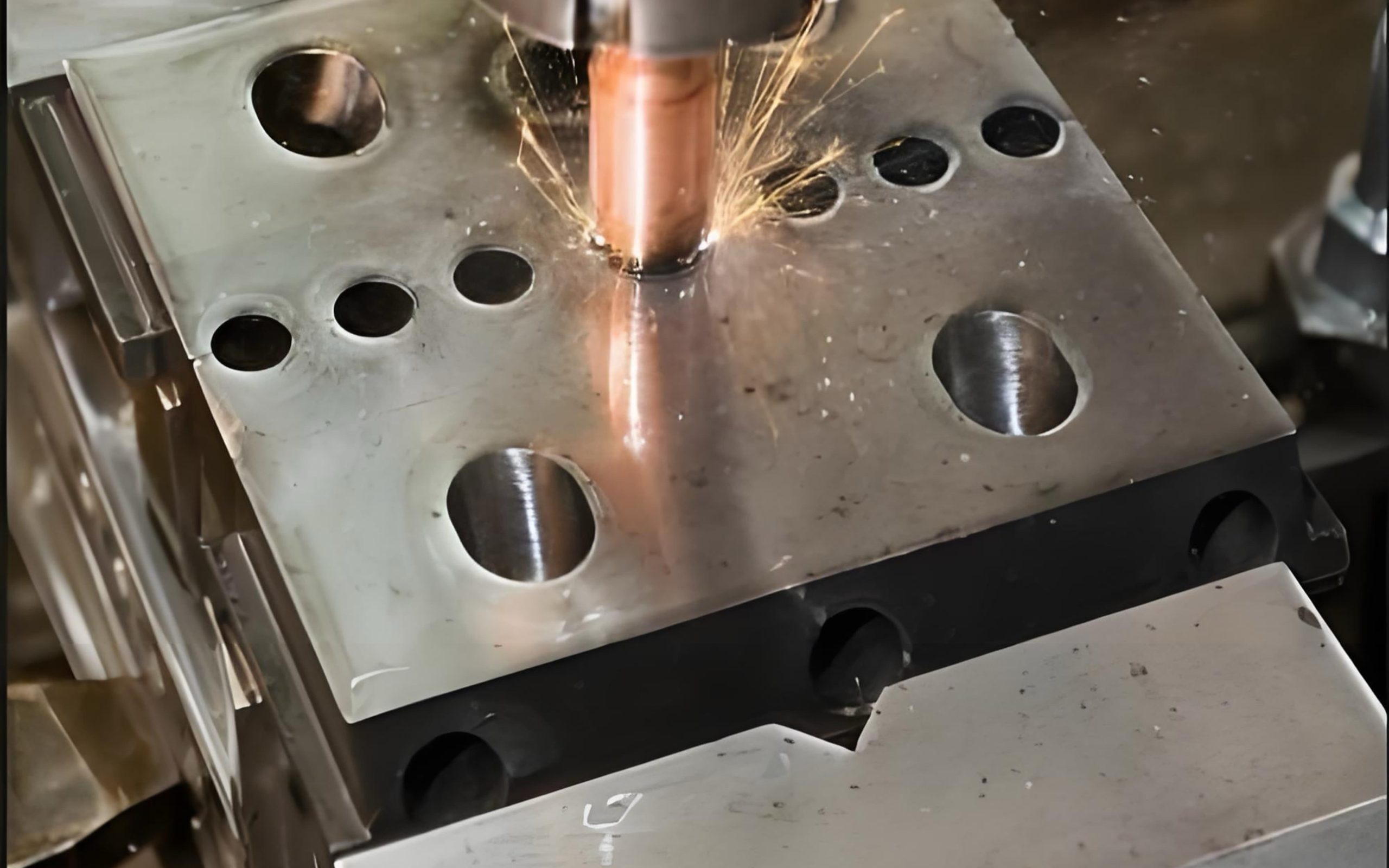
Problem manifestation
- Dust or particles still remain on the mold surface after sandblasting or polishing.
- lmpurities affect the effect of subsequent coating or processing steps.
Cause analysis
- Ordinary glass beads or inferior media are used, and the cleaning efficiency is low.
- Improper sandblasting parameters, unoptimized spray angle or pressure, and impurities cannot be completely removed.
- Lack of subsequent cleaning steps or unstandardized processes.
Insufficient material fluidity
Problem manifestation
- During the injection molding process, the material cannot fill the mold cavity, resulting in incomplete part molding.
- Problems such as insufficient filling pressure, cold material marks or welds appear in the mold.
Cause analysis
- Too rough or too glossy surface changes the flow path of the material and increases resistance.
- Runner design defects: improper gate position and size, and insufficient optimization of material filling efficiency.
- Uneven cooling causes premature solidification of the material.
Решение
Preparation before processing
- Material pretreatment to ensure that the material is fully dry before injection molding and control the moisture content.
- Use software to optimize texture and flow channel design to ensure uniform flow and texture consistency.
Process optimization
- Combined with five-axis machining technology, adjust path spacing, reduce tool marks, and improve surface uniformity.
- Use high-speed milling technology to optimize feed and speed ratio and finely control processing quality.
- Upgrade equipment, high-precision CNC machine tools and laser engraving technology to improve complex texture and detail processing capabilities.
- Real-time detection of tool wear and timely replacement to ensure processing stability.
Post-processing cleaning and surface treatment
- Use ceramic sandblasting beads and other media to sandblast to remove processing residues and ensure smoothness.
- Add ultrasonic cleaning or gas purging to completely remove tiny impurities.
- Combined with mirror polishing or sandblasting for strengthening treatment, further improve surface durability and reduce microcracks.
Demolding and subsequent optimization
- Adjust the mold slope, add auxiliary textures, optimize demolding performance, and avoid adhesion problems.
- Add anti-stick coatings to key parts to reduce friction coefficients and improve demolding efficiency.
- Use a zoned temperature control system and optimize vent design to reduce uneven cooling and bubble problems.
Process verification and improvement
- Optimize the runners and gates to ensure that the material is fully and evenly filled.
- Final test: Evaluate the actual use of the mold to ensure that the texture, finish and functionality fully meet the requirements.
Sandblasting media help achieve surface finish
In the mold finishing process, sandblasting is an indispensable technology that can effectively make up for the shortcomings of other processing methods and optimize the surface quality. Especially in solving tiny processing textures, impurity residues and surface defects, the selection of sandblasting media is particularly critical. Among them, ceramic sandblasting beads have become an ideal choice for improving the surface finish of molds with their excellent performance. Its advantages are as follows:
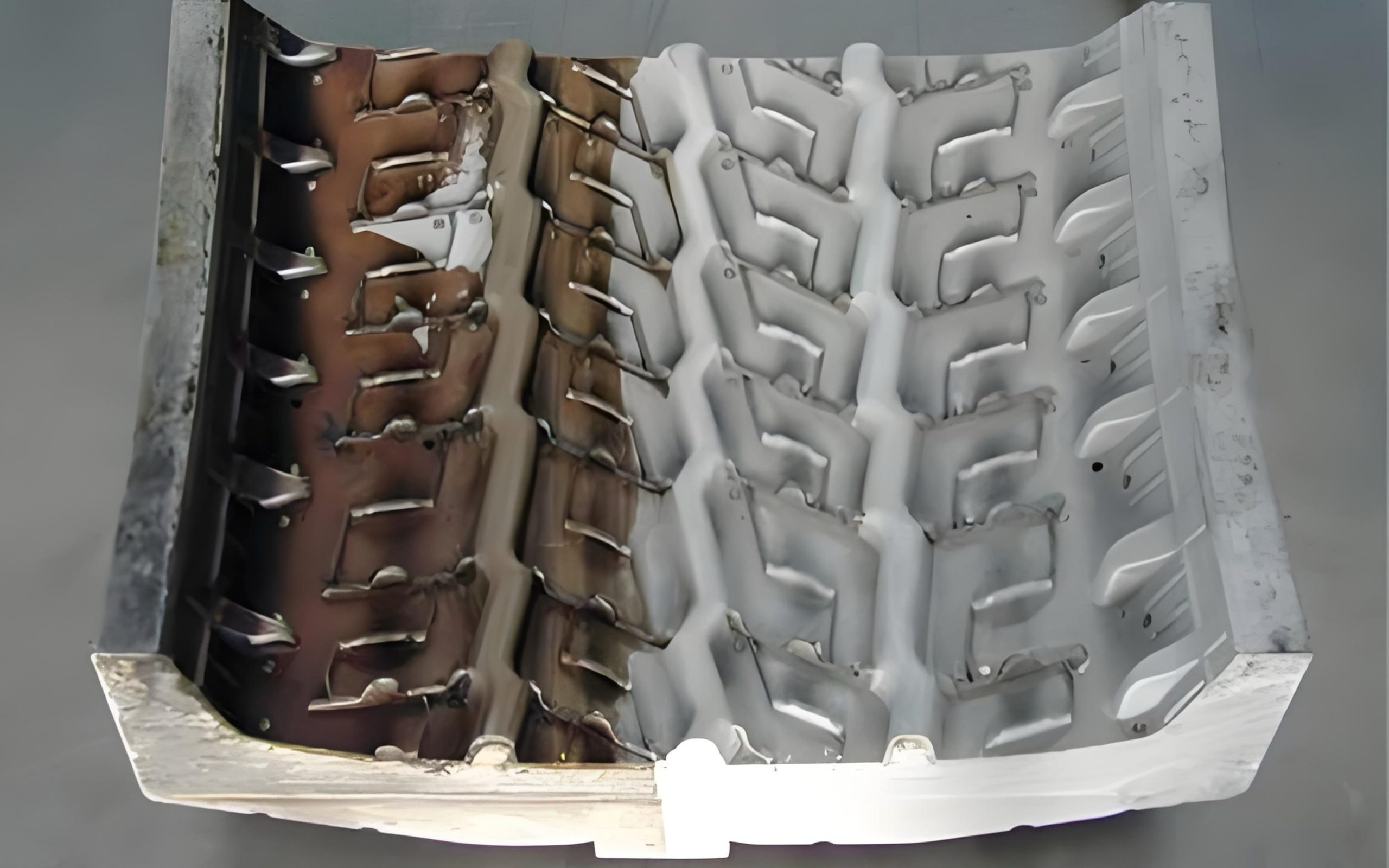
Remove microcracks and processing textures. Ceramic beads have high Mohs hardness and uniform particles. They can effectively eliminate microcracks and textures left by tool processing without damaging the mold surface, and optimize the finish.
Improve surface consistency. Ceramic media has a uniform density distribution and consistent size, which can evenly cover the mold surface to avoid functional and appearance problems caused by uneven texture or excessive local roughness.
Reduce adhesion problems. Ceramic beads have good surface smoothness and low dust characteristics, which can effectively reduce the friction coefficient of the mold surface and reduce the damage caused by adhesion of the material during the demolding process.
Improve the durability of the workpiece. Sandblasting can also strengthen the mold surface, improve its fatigue strength and corrosion resistance, and extend the life of the mold.
Optimize the working environment. Compared with traditional glass beads, ceramic sandblasting beads have less dust, which not only improves processing accuracy but also reduces health risks.
By combining the advantages of ceramic sandblasting beads, mold manufacturers can not only significantly improve the surface finish, but also effectively avoid common problems such as cracks, surface impurities, and demolding difficulties, providing customers with high-performance mold solutions.
If you need more detailed sandblasting process and media recommendations, you can find us for further discussion.
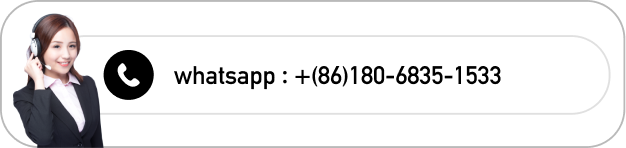