Керамические шарики или стальная крошка: Что лучше для абразивной очистки?
7 января 2025 года
Пескоструйная обработка играет важную роль в современном производстве и обслуживании. Она не только обеспечивает гладкую основу для последующей покраски или другой обработки поверхности, но и эффективно улучшает механические свойства и внешний вид поверхности.
При пескоструйной обработке очень важно правильно выбрать пескоструйный материал. Хотя стальная крошка уже давно широко используется в качестве традиционного средства для пескоструйной обработки, керамические абразивы постепенно превзошли стальную крошку во многих из тех же областей применения благодаря своим превосходным характеристикам. В этой статье мы подробно сравним эти два специальных пескоструйных материала, чтобы помочь читателям сделать наиболее правильный выбор при практическом применении.
Керамические бусины
Относительно новый вид пескоструйного материала, он постепенно получает широкое распространение по мере роста потребности промышленности в тонких, экологически чистых и долговечных пескоструйных материалах. Пескоструйный материал с оксидом циркония и другими высокоизносостойкими материалами в качестве основных компонентов, уникальный процесс производства, благодаря которому он имеет однородную сферическую структуру и твердую текстуру, что может обеспечить эффективный эффект очистки при обработке поверхности заготовки.
Характеристики товара
- Сферическая форма, давление, создаваемое в процессе пескоструйной обработки, является относительно равномерным, что позволяет эффективно уменьшить повреждения поверхности.
- Низкое образование пыли необходимо для защиты окружающей среды и здоровья операторов.
- По сравнению с другими пескоструйными материалами, он имеет более длительный срок службы и может быть переработан многократно, что снижает затраты на долгосрочное использование.
- Высокая твердость (твердость по Моосу 9) и умеренная сила удара дают ему значительные преимущества в эффективном удалении покрытий, чешуек, масляных пятен и т.д.
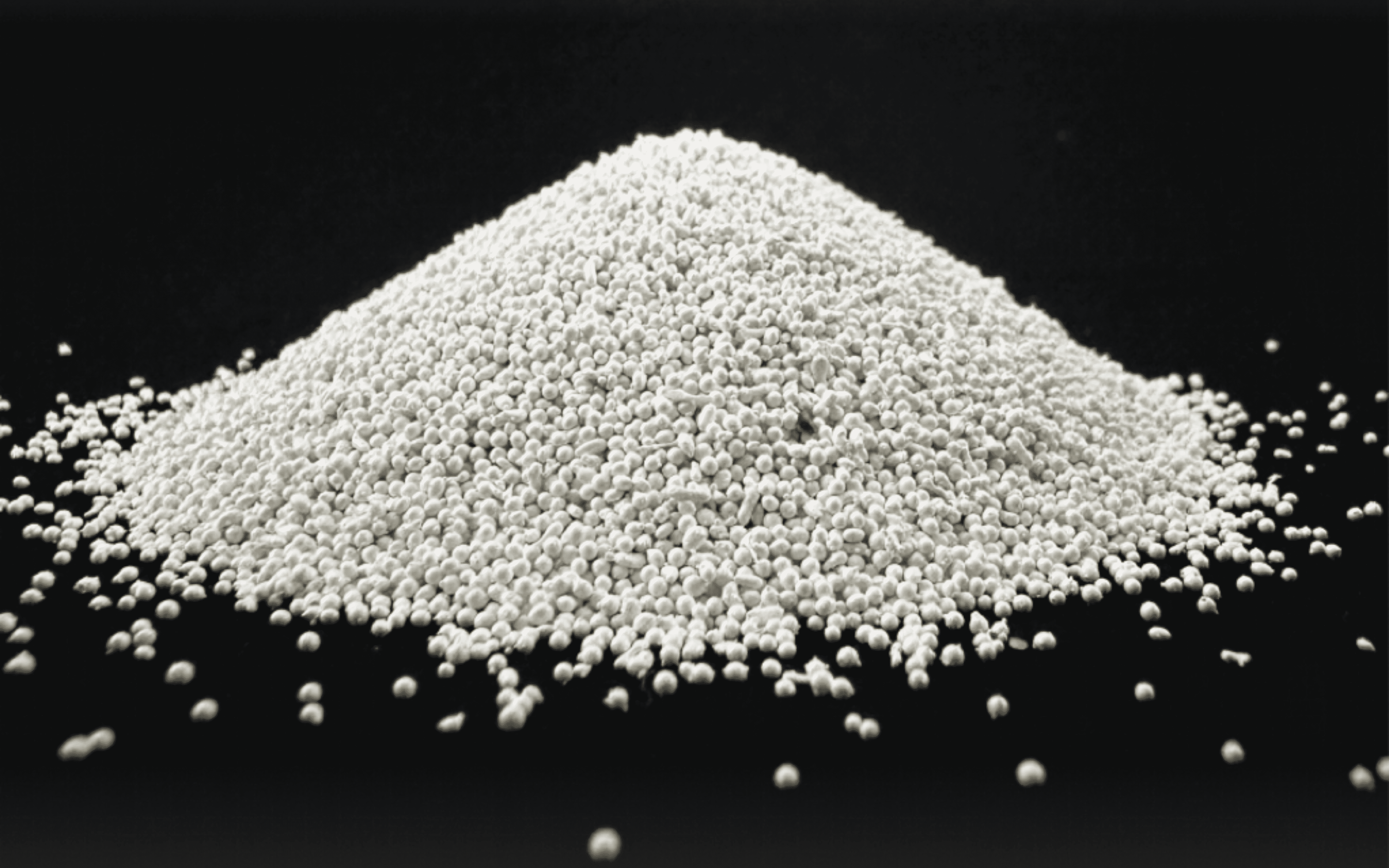
Стальная крошка
Это традиционное средство для пескоструйной обработки, которое сыграло свою роль в ранних промышленных применениях, таких как обработка металлических поверхностей. Благодаря своим высоким ударным характеристикам она стала важным материалом для обработки поверхности в процессе пескоструйной обработки. Частицы стальной крошки относительно грубые и имеют неправильную угловатую форму. По сравнению с керамическими абразивными шариками она имеет меньший срок службы и требует более частой замены.
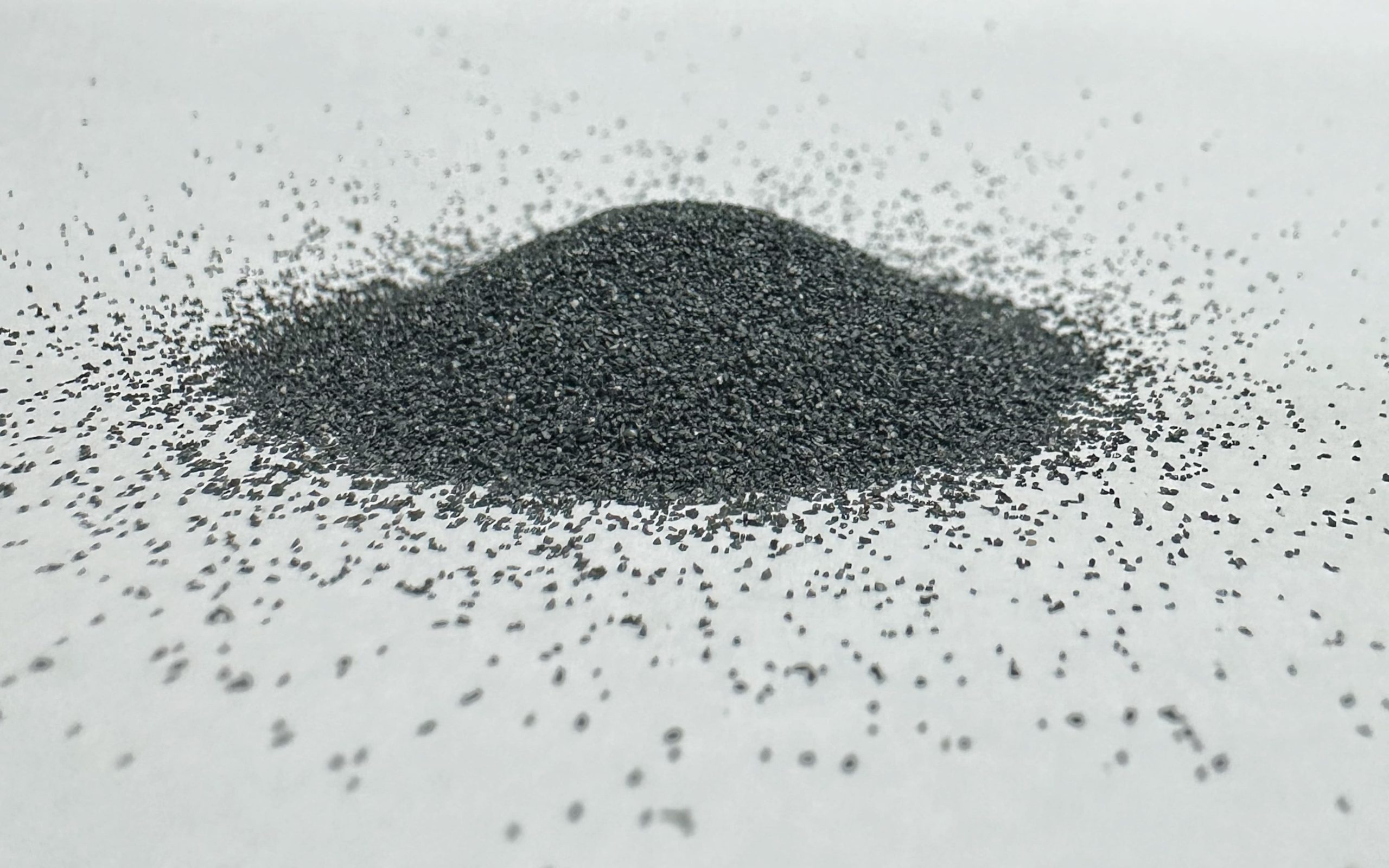
Характеристики товара
- Угловая структура обеспечивает более сильное воздействие в процессе пескоструйной обработки, что подходит для удаления сильной ржавчины, стойких покрытий и т.д.
- Стальная крошка обычно дешевле керамических абразивных шариков, а низкая стоимость подходит для проектов с ограниченным бюджетом и большими масштабами.
- Благодаря своей высокой ударопрочности стальная крошка оставляет на поверхности заготовки шероховатую текстуру, которая способствует адгезии покрытия.
Области применения стальной крошки и керамических шариков
Электронные компоненты
- Полупроводниковые пластины
- Печатные платы
- Разъемы и штекеры
- Корпуса датчиков
Автозапчасти
- Компоненты двигателя
- Тормозные диски и колодки
- Части тела
- Компоненты выхлопной трубы
- Детали системы рулевого управления
Медицинские изделия
- Хирургические инструменты
- Имплантаты
- Катетеры
- Корпуса медицинских насосов
- Иглы и мелкие медицинские детали
Формы
- Формы для литья под давлением
- Формы для литья
- Формы для штамповки
- Формы для литья под давлением
Аэрокосмическая промышленность
- Лопатки турбины
- Оболочки фюзеляжа
- Колеса самолетов
- Корпуса для авионики
- Детали двигателя
Судовые части
- Пропеллеры
- Стыки корпуса
Запчасти для промышленного оборудования
- Корпуса насосов и клапаны
Преимущества керамических абразивных материалов
Керамический абразивный бисер демонстрирует значительные преимущества при пескоструйной очистке. Эти характеристики делают их лучше традиционной стальной крошки в вышеуказанных сценариях применения. Ниже подробно описаны уникальные преимущества керамических абразивных материалов с точки зрения экологических характеристик, срока службы, поверхностного эффекта и т. д.
Экологические характеристики: меньшее образование пыли
Согласно данным экологических исследований Немецкой промышленной ассоциации, пылеобразование керамических абразивов в реальных условиях эксплуатации более чем на 80% меньше, чем у стальной крошки, как показано ниже:
- Керамические бусины: концентрация пыли составляет около 0,2 мг/м³
- Стальная крошка: концентрация пыли достигает 1 мг/м³
Это не только соответствует стандартам безопасности OSHA (Occupational Safety and Health Administration), но и значительно снижает частоту обслуживания оборудования для удаления пыли.
Срок службы: повышенная эффективность цикла
Данные измерений показывают, что керамические абразивные материалы могут быть переработаны в среднем 35 раз и до 50 раз в высокоинтенсивных пескоструйных работах, в то время как срок службы стальной крошки обычно составляет 7-10 раз.
Сравнительный эксперимент, проведенный авиационной компанией, показал, что керамические шарики могут обрабатывать в 4 раза большую площадь поверхности на килограмм стальной крошки и при этом сохранять более 70% от своей первоначальной эффективности после многократного использования.

Поверхностный эффект: более равномерное качество обработки
Данные, предоставленные Международной лабораторией обработки материалов, показывают, что керамические абразивные материалы позволяют более точно контролировать шероховатость поверхности заготовок после пескоструйной обработки, что подходит для сценариев с высокими требованиями:
- Производство пресс-форм: Шероховатость Ra поверхности пресс-формы, обработанной керамической абразивной средой, равномерно распределена в диапазоне 0,3-0,5 мкм, в то время как у стальной крошки она сильно колеблется и может составлять 1-2 мкм.
- Керамические абразивные шарики позволяют получить равномерный матовый эффект на поверхности титанового сплава, сохраняя при этом биосовместимость материала.
Безопасность эксплуатации: низкая сила удара уменьшает повреждение поверхности
Эксперименты показали, что сила удара керамических шариков составляет всего 50% от силы удара стальной крошки, что наглядно проявляется следующим образом:
- После пескоструйной обработки поверхности алюминиевых деталей глубина вдавливания керамических абразивных материалов составляет 10 мкм, в то время как глубина вдавливания стальной крошки достигает 30 мкм, что значительно повышает риск повреждения материала.
- При обработке поверхностей прецизионного оборудования (например, лопаток аэрокосмических турбин) керамические абразивные материалы позволяют значительно уменьшить количество микротрещин и сократить количество переделок примерно на 30%.
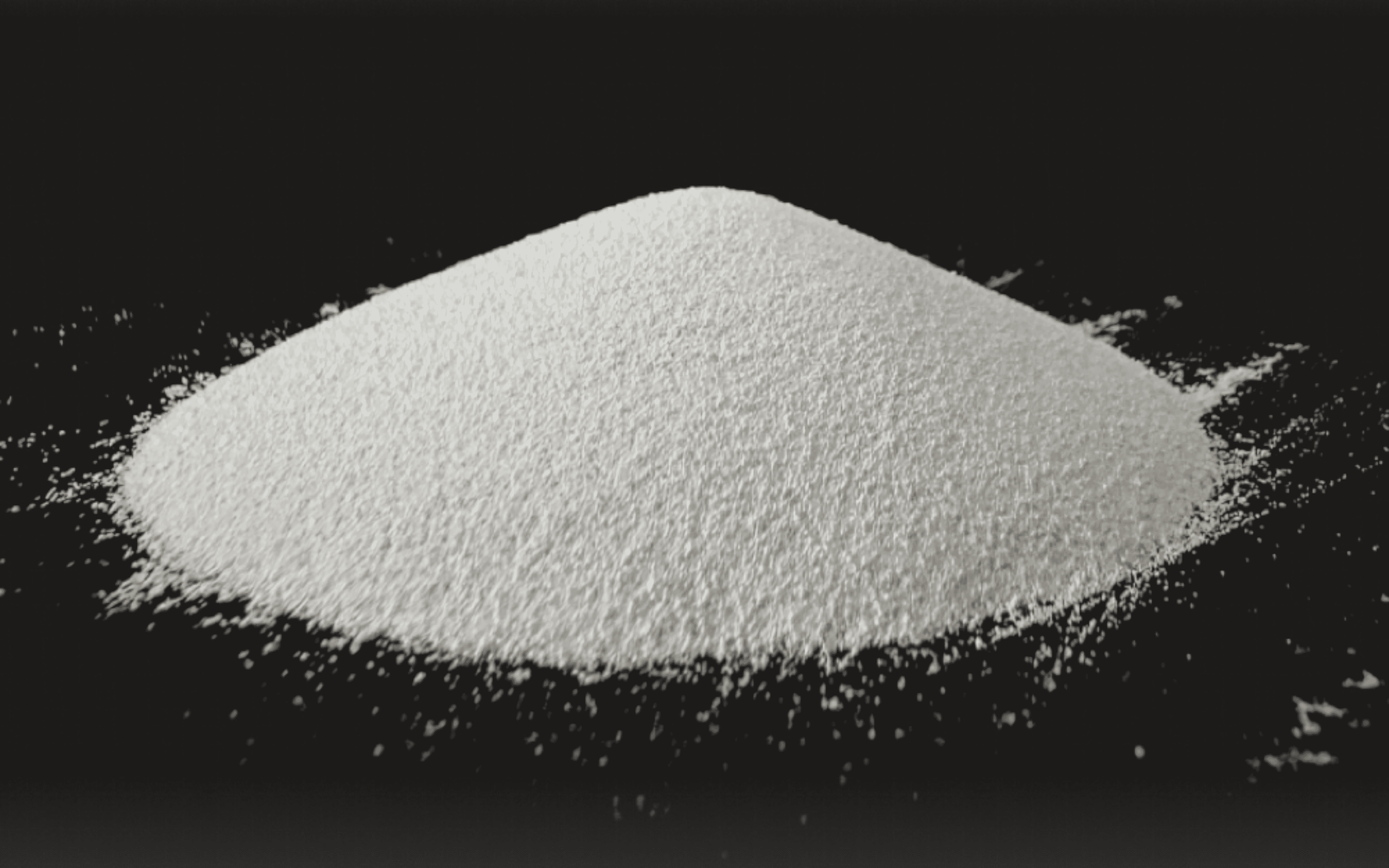
Высокая адаптивность: широкий спектр применения
По отзывам клиентов, керамические абразивные шарики широко используются в следующих подложках и особых сценариях:
- Металлические подложки: используется для очистки и полировки поверхностей титановых сплавов и сплавов на основе никеля в авиационной промышленности.
- Пластиковые подложки: обеспечивают мягкую текстуру при обработке поверхностей автомобильных деталей интерьера (например, приборных панелей и дверных обшивок), заменяя традиционные процессы химической очистки.
- Керамические и стеклянные подложки: достижение тонкой текстуры, например, травление промышленных зеркал.
Экономические преимущества: снижение общих эксплуатационных расходов
Согласно фактическим данным, компании, использующие керамические абразивные материалы, могут экономия до 25%-40% затрат каждый год, в основном за счет:
- Затраты на обслуживание оборудования: низкое пылеобразование снижает частоту очистки системы фильтров, продлевает срок службы и снижает затраты на обслуживание примерно на 20%.
- Экономия трудозатрат: эффект обработки поверхности керамическими абразивными материалами более тонкий, не требуется дополнительной вторичной обработки, а время работы сокращается на 15%-25%.
- Долгосрочные инвестиции в материал: несмотря на более высокую первоначальную стоимость, среднее время использования каждой тонны керамической абразивной смеси примерно в 3 раза дольше, чем стальной крошки.
Преимущества стальной крошки
Как традиционный и широко используемый пескоструйный материал, стальная крошка уступает керамическим абразивным шарикам по всем параметрам, но по-прежнему занимает важное место во многих промышленных областях благодаря своей уникальной высокой прочности и экономичности.
Высокая сила удара: быстрое удаление стойких поверхностных загрязнений
- При удалении толстых слоев ржавчины, твердых оксидных чешуек и многослойных покрытий стальная крошка способна за короткое время произвести сильный ударный эффект и быстро удалить поверхностные загрязнения.
- Угловая структура частиц еще больше повышает эффективность резки и особенно подходит для очистки поверхности высокопрочных материалов. В проектах по удалению ржавчины с поверхностей мостов, кораблей и тяжелого оборудования часто предпочитают использовать стальную крошку.
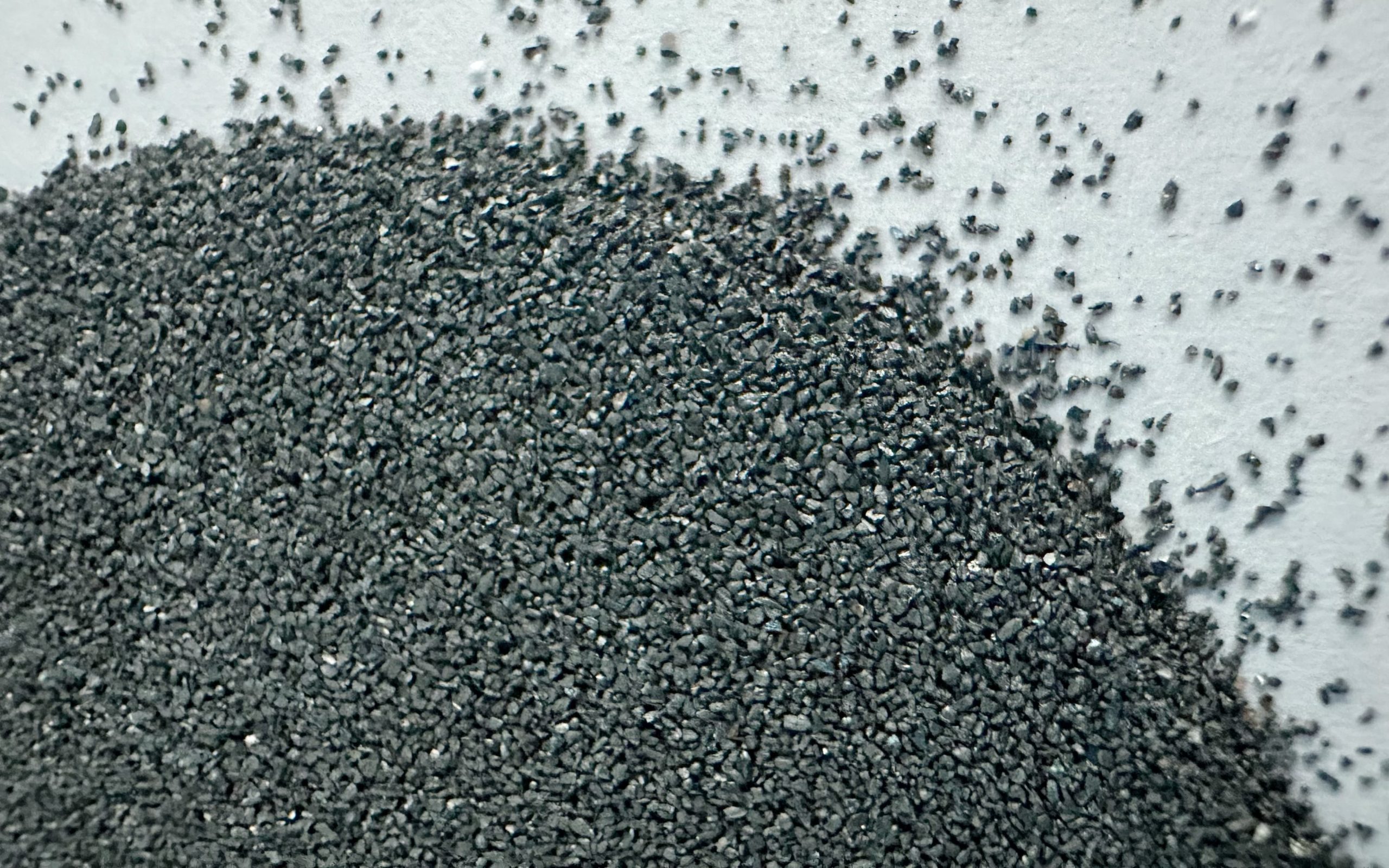
Экономичность: низкая цена материала
-
По сравнению с такими дорогостоящими материалами, как керамические шарики, первоначальная стоимость стальной крошки относительно невысока и обычно составляет от 1/3 до 1/2 стоимости керамических абразивных материалов, что особенно удобно для крупных проектов с ограниченным бюджетом.
-
Даже если его нужно часто заменять, общая стоимость материала остается весьма конкурентоспособной благодаря его низкой цене.
Несколько вариантов размера частиц: удовлетворение различных технологических требований
- Стальная крошка может иметь различные характеристики размера частиц в соответствии с требованиями приложения, начиная от ультратонких частиц и заканчивая крупными частицами:
Крупнозернистая стальная крошка подходит для удаления сильных загрязнений и создания шероховатой текстуры поверхности, обеспечивающей более прочное сцепление с последующим покрытием.
Мелкозернистая стальная крошка используется для относительно тонкой обработки поверхностей, например, для легкого шлифования и предварительной обработки металлических поверхностей.
- Например, в авторемонтной промышленности крупнозернистая стальная крошка используется для предотвращения ржавчины и очистки шасси, а мелкозернистая - для пескоструйной обработки поверхности кузова.
Превосходные механические свойства: высокая твердость и прочность
- Стальная крошка обладает высокой твердостью (обычно в диапазоне 40-65 HRC) и высокой прочностью. Она способна выдерживать высокоинтенсивные удары и при этом легко ломаться. Она особенно подходит для обработки таких высокотвердых материалов, как углеродистая сталь, нержавеющая сталь и чугун.
- Даже в условиях высоких температур характеристики стальной крошки остаются стабильными, не размягчаясь и не разрушаясь.
Низкий технический порог: возможность адаптации к различным видам оборудования
- Большинство пескоструйного оборудования, представленного на рынке, поддерживает стальную крошку в качестве носителя, не требуя дополнительных затрат на модификацию оборудования.
- Оборудование имеет низкую стоимость использования, особенно подходит для малых и средних предприятий и подрядчиков проектов.
Хорошая износостойкость: подходит для многократного использования
- Хотя количество циклов работы стальной крошки не так велико, как у керамических шариков, ее износостойкость по-прежнему конкурентоспособна среди традиционных средств. Единичный срок службы составляет около 7-10 раз, что достаточно для удовлетворения потребностей средне- и краткосрочных проектов.
- Эксперименты показали, что скорость потери объема высококачественной стальной крошки при нормальных условиях эксплуатации составляет менее 1,5%, что свидетельствует о хорошей долговечности.
Широкое признание на рынке
- Процесс производства стальной крошки отработан, цепочка поставок совершенна, и ее можно легко купить по всему миру.
- Операторы, как правило, знакомы с работой и использованием стальной крошки, что сокращает расходы на обучение.
Реферат: Как правильно выбрать пескоструйный материал?
Стальная крошка и керамические абразивные шарики, являющиеся двумя основными рабочими средами в области пескоструйной очистки, обладают значительными преимуществами. Их применимость зависит от конкретных требований, характеристик заготовки и бюджетных ограничений.
В реальных промышленных условиях стратегия пескоструйной обработки "сначала грубая, а затем тонкая" является распространенным и эффективным решением. Сочетание стальной крошки и керамических абразивных шариков позволяет в полной мере использовать характеристики обоих материалов:
- Предварительное лечение: Используйте стальную крошку для высокоэффективной предварительной очистки, чтобы быстро удалить большие участки ржавчины или толстых покрытий, заложив прочную основу для последующей обработки.
- Аффинажная обработка: Используйте керамические абразивные шарики для полной гомогенизации и рафинирования поверхности, улучшения качества поверхности и достижения более высоких визуальных и функциональных требований.
Такая стратегия позволяет не только сократить время обработки, но и найти идеальный баланс между экономичностью и эффективностью. Например, при обслуживании судов стальная крошка позволяет быстро очистить стойкую грязь на обшивке корпуса, а керамические шарики используются для детальной обработки гребных винтов или прецизионных деталей.
Пользователи могут гибко выбирать или комбинировать стальную крошку и керамическую абразивную среду в соответствии с конкретными требованиями проекта. В реальных условиях эксплуатации постоянная корректировка параметров процесса и комбинирование сред - это ключ к удовлетворению различных потребностей. Надеюсь, эта статья даст вам четкое представление о том, как выбрать подходящую абразивную среду!
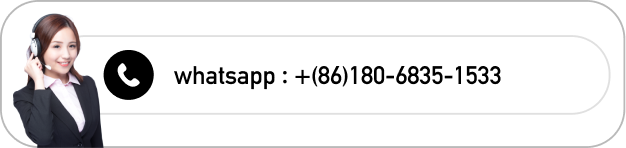